Leather Upper Manufacturing Factories are Facing Production Challenges.
When I arrived at the client’s facility, the production team grappled with several issues. Their traditional cutting methods involved manual labor and outdated machinery were causing inefficiencies. The team struggled with inconsistent cut quality, excessive material waste, and high labor costs. Additionally, the lack of flexibility in their existing setup made handling different leather types and thicknesses challenging, especially when switching between designs or materials.
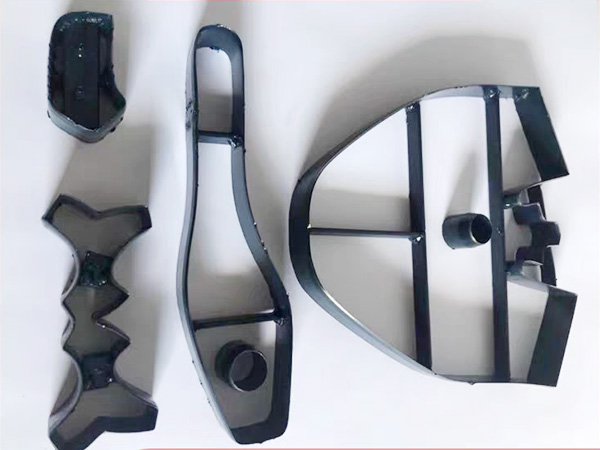
The AMOR CNC Solution for Leather Upper Cutting
After carefully assessing the situation, I introduced the AMOR CNC Leather Upper Cutting Machine as a comprehensive solution. Here’s how it addressed the challenges:
Dual-Head Cutting Efficiency:
I demonstrated the machine’s dual-head cutting mode. In asynchronous mode, the two cutting tools could work on different patterns simultaneously, speeding up the production process without sacrificing precision. Alternatively, in synchronous mode, both heads cut identical patterns, doubling the output and maximizing the machine’s efficiency. This flexibility allowed the client to optimize production according to their specific needs.

High-Frequency Oscillating Tools:
The client was particularly impressed by the machine’s high-frequency oscillating cutting tools. These tools provided fast, accurate cuts without the need for traditional molds. This not only reduced setup time but also allowed for quick changes between different designs. Whether they were cutting 24 or 44 pieces per shoe, the machine handled multiple layers of ultra-fine leather effortlessly, accommodating up to 8 layers in a single pass.
Precision and Clean Cutting:
One of the key concerns at the factory was the quality of cuts, especially when working with white leather, which is prone to discoloration if not handled properly. Unlike their previous laser cutting machine, which often left burnt edges and smoke residue, the AMOR CNC machine delivered clean, precise cuts with no smoke or yellowing. This was a game-changer for their production, particularly for premium products where quality is non-negotiable.

Advanced Automation and Nesting:
I showed them how the machine’s infrared positioning system and automated nesting software could further enhance their productivity. The software allowed for one-click graphic imports, and the computer automatically optimized the layout to maximize material usage. This meant less waste and more efficient cutting, all without the need for expensive and time-consuming mold preparation.
Additional Tooling for Punching:
The client also needed punching holes in the leather uppers. I demonstrated how our machine could be equipped with a punching tool, enabling it to complete both cutting and punching operations in one smooth, continuous process. This addition not only streamlined their workflow but also increased overall production efficiency.
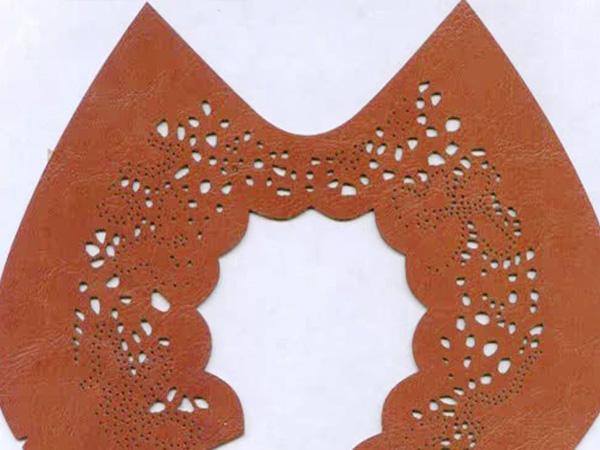
Secure Multi-Layer Cutting:
To ensure the best results when cutting multiple layers of leather, we utilized a secondary film overlay technique. This method securely fixed the material to the work table, preventing any shifting during the cutting process. The result was a smooth, uninterrupted cut, with perfectly aligned layers—essential for maintaining product quality in multi-layer designs.
Cost-Effective and Scalable Production:
Finally, I compared the AMOR CNC machine with their existing die-cutting setup. The new machine eliminated the need for expensive die molds, reduced material wastage, and lowered labor costs. In fact, it could replace two traditional die-cutting machines, with a daily output ranging between 7,000 and 10,000 cuts. This scalability made it an ideal solution for both small-scale bespoke orders and large-scale production runs.

Conclusion
By the end of the visit, the client was convinced that the AMOR CNC Leather Upper Cutting Machine was the right choice for their business. It provided a flexible, efficient, and cost-effective solution that met their production needs and could easily adapt to future demands.
As an engineer, it’s always rewarding to see how our technology can make a tangible difference in a customer’s operations. The AMOR CNC Leather Upper Cutting Machine is more than just a piece of equipment; it’s a comprehensive solution designed to elevate your production process, improve quality, and reduce costs. Whether you’re producing high-end footwear or other leather goods, this machine is built to meet the challenge of modern manufacturing.
