Why Customization Matters for Production Efficiency?
In today’s fast-paced production world, flexibility is key. Gone are the days of one-size-fits-all cutting solutions. As manufacturers, we need to cater to specific client requirements, often with tight deadlines. That’s why having a machine that allows you to customize its settings is like having a secret weapon. It improves your workflow, boosts efficiency, and makes you look like a rockstar to your customers.
Take a look at the industries we serve: gasket manufacturing, packaging, and insulation. All of them benefit from the flexibility to switch between different materials and cutting techniques. Data shows that companies using customizable machines are 40% more productive compared to those stuck with fixed settings.
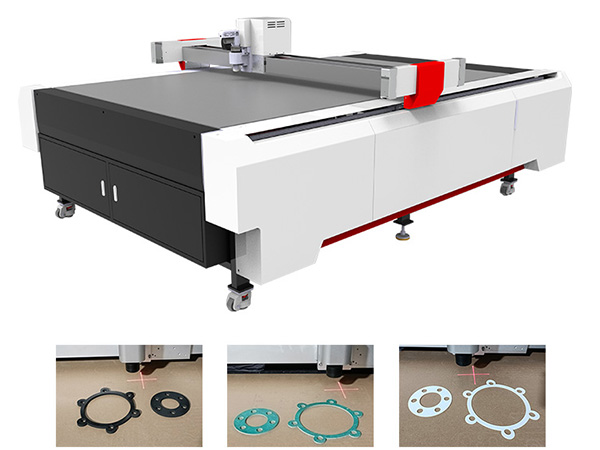
How to Adjust Speeds Based on Material?
Here’s where things get interesting: not all materials are created equal. For instance, cutting soft EVA foam requires a much lower speed than cutting tough rubber sheets. You can adjust the cutting speed directly from our machine’s interface. For example, when working with foam packaging materials, I set the speed between 200-300mm/s, but for harder materials like rubber, I crank it down to 100-150mm/s.
This isn’t just guesswork. We’ve built-in presets based on material types, or you can fine-tune it yourself. Why does this matter? Using the wrong speed for a specific material can ruin the cut, slow production, or worse, damage the machine.
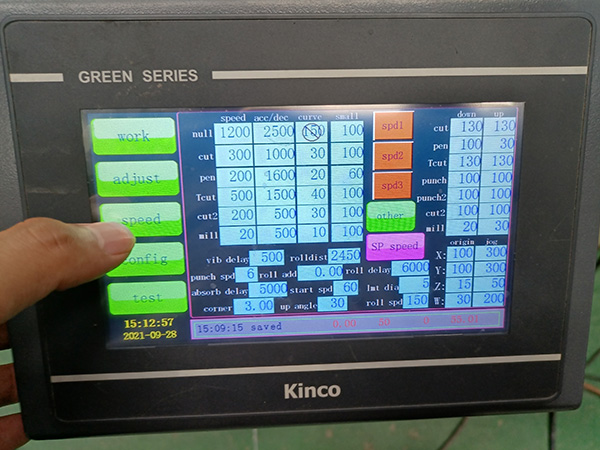
Can I Swap Out Cutting Tools for Different Jobs?
Absolutely. One of the best features of our machines is the ease of tool swapping. Imagine being able to switch from an oscillating knife to a milling cutter in just a few minutes. This tool flexibility is a huge time-saver, especially when you’re dealing with multiple materials in a single production run.
For instance, the Pneumatic Oscillating Tool is perfect for cutting flexible materials like rubber or felt, while the Milling Cutter Tool handles thicker, more rigid materials like high-density foam or composites. These tools are designed to work in harmony with the machine, making the cutting process smoother and faster. Research shows that multi-tool configurations improve production efficiency by up to 50%.

What Role Do Cutting Depth and Pressure Settings Play?
The beauty of our CNC gasket cutting machines lies in their ability to customize both the cutting depth and the pressure applied during the cut. Why is this important? Well, different materials have different thicknesses and densities, so you don’t want to apply the same pressure or depth to, say, both a 2mm graphite gasket and a 10mm phenolic air duct.
For materials like high-density EVA foam, I’ll usually increase the pressure and adjust the depth to ensure a clean cut without having to repeat the process. On the flip side, thinner materials like paper-based gaskets need less pressure but more precision, which our machine handles with ease.

Are There Any Safety Concerns with Custom Settings?
One of the questions I hear a lot is, “Does customizing machine settings pose any safety risks?” The short answer is no, as long as you’re following standard operating procedures. Our machines are equipped with automatic safety features, including a built-in sensor system that shuts down the machine if something goes wrong. No need to worry about safety. Customization doesn’t just make production more efficient; it also keeps things safe by preventing mistakes like over-cutting or material slippage.
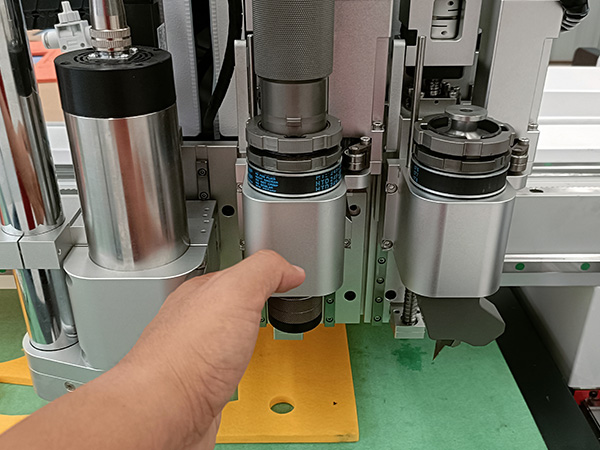
How Do I Customize My Machine for Complex Production Runs?
If you’re running complex jobs, you’ll love the automation options. Our machines let you pre-program specific settings for different materials and designs, so all you need to do is load the file, hit start, and watch the magic happen. This is particularly useful for businesses like Jack’s, where custom gasket orders vary daily.
What’s more, switching between mass production and small-batch runs is a breeze. With customizable tool paths and settings, you can quickly change from cutting 1000 units of identical gaskets to making five bespoke pieces without losing any time.
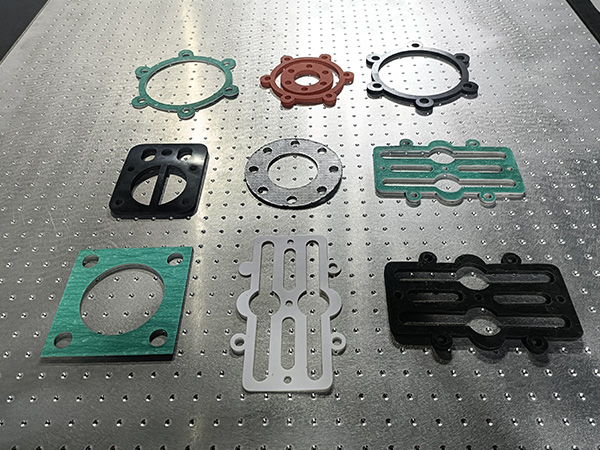
Conclusion
In short, the ability to customize machine settings for different production needs isn’t just a nice to have; it’s essential for any business that values efficiency and precision. Whether you’re adjusting speed, depth, or swapping out tools, our AMOR CNC gasket cutting machines have you covered.
Ready to get your hands on a machine that truly adapts to your needs? We’ve got you. Let’s make production easy, efficient, and, dare I say, fun.