1. Key Factors to Consider When Choosing a Cutting Machine
Let’s start by looking at the main things that matter when picking out a cutting machine for acoustic panels.
Material Compatibility: What Do You Need to Cut?
Different materials, like polyester fiber acoustic panels, fiberglass cotton, and felt, all have their own unique cutting needs. Ideally, you want a machine that can handle a range of materials. This way, you get the most flexibility without needing multiple machines. So, think about what materials you work with most often and pick a cutting machine that can tackle them all.

Cutting and Grooving Precision: Why Does It Matter?
Here’s the thing—if you want those clean, burr-free edges and precise grooves in your acoustic panels, the machine’s precision needs to be top-notch. The cutting dimensions and groove depths should remain consistent throughout production, so it’s important to check the machine’s mechanical structure and installation process before making a decision.
Take a look at this comparison chart to help you understand the factors that influence cutting precision:
Feature | Single Motor Drive | Dual Motor Drive | Standard Motor | Servo Motor | Belt Drive | Rack and Pinion Drive | Gear Reducer | Speed Reducer |
---|---|---|---|---|---|---|---|---|
Precision | Low | High | Medium | High | Medium | High | High | Medium |
Power & Efficiency | Medium | High | Medium | High | High | High | Medium | High |
Maintenance Cost | Low | Medium | Medium | High | Low | Low | High | Medium |
Cutting Speed and Efficiency: Time Is Money!
Cutting speed directly impacts your production efficiency. The faster the machine, the more panels you can produce in a shorter amount of time. If you’re comparing a CNC oscillating knife cutting machine with other methods like laser cutting, here’s how they stack up:
Cutting Method | Speed (mm/s) | Efficiency (Panels/hour) | Notes |
---|---|---|---|
Laser Cutting | 80-120 | Low | Slower speeds, heat distortion |
Oscillating Knife | 260-450 | High | Faster, no heat damage |
As you can see, oscillating knife cutting machines are far faster and more efficient, which is crucial for mass production.
Flexibility for Custom Shapes: Tailored to Your Needs
If your acoustic panels have complex shapes or designs, you need a cutting machine that can adapt. A good CNC cutting machine should let you cut custom shapes, add grooves, or even make angled cuts. So, flexibility is key here. Look for a machine that can handle everything from basic cuts to intricate, custom designs with ease.
Ease of Operation: No Need for PhD in Engineering
The easier the machine is to operate, the quicker you can get to work. A machine with a user-friendly interface means less training time, and it’s easier for your operators to get the hang of it. Let’s face it—complicated machines can lead to frustration and mistakes, so the simpler, the better!
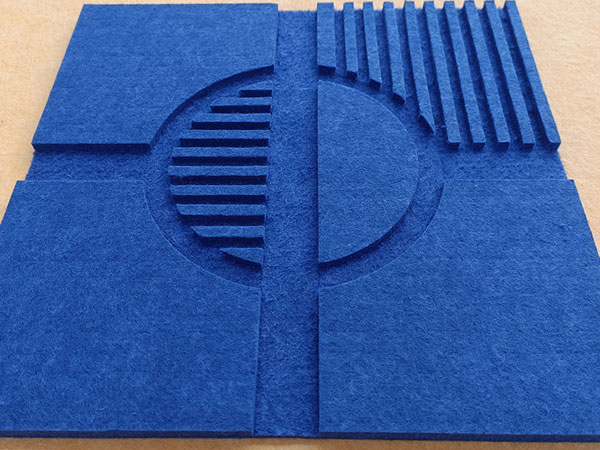
2. Why Choose CNC Oscillating Knife Cutting Machines for Acoustic Materials?
Now that we’ve covered the key factors, let’s talk about why CNC oscillating knife cutting machines are the ideal choice for cutting acoustic materials.
1. Material-Friendly: No Heat, No Problem
CNC oscillating knife machines use high-frequency vibrations to cut materials. This means no heat is generated during cutting, which is perfect for sensitive acoustic materials. Unlike laser cutting, which can scorch the edges and warp materials, oscillating knife machines ensure smooth, clean cuts without any thermal damage.
2. Eco-Friendly and Safe
Laser cutting produces harmful gases, and let’s not forget about the potential health risks to your team. Oscillating knife cutting doesn’t create any toxic gases, and it also avoids the dust and fumes created by traditional engraving or milling methods. It’s a win-win for both the environment and your employees.

3. Smart and Adaptable
The beauty of a CNC oscillating knife cutting machine is its modular design. Depending on the material you’re cutting, you can easily swap out tool holders and adjust the machine for different cutting tasks. It’s like a one-size-fits-all machine for various material thicknesses and cutting needs—cut, groove, carve, or even mark, all with a single machine.
4. High-Speed and Efficient
As mentioned earlier, the speed is a major advantage of oscillating knife machines. For instance, cutting 9mm-12mm polyester fiber panels with an oscillating knife can reach speeds of 260-450mm/s. In comparison, a laser cutter is much slower, running at only 80-120mm/s.
3. How to Choose the Right Tool for the Job
Each cutting task may require different tools. Here’s a quick breakdown of the most commonly used tools for acoustic panels:
Tool | Best For | Features |
---|---|---|
High-Frequency Electric Knife | 9-15mm thick polyester fiber panels | Fast cutting, smooth edges |
Pneumatic Oscillating Tool | Thicker, denser materials (20-50mm) | Cuts tough materials like fiberglass and felt |
Bevel Cutting Tool | Angled cuts and grooves | 5°, 10°, 15°, 30°, 45° angles |
Milling Cutter Tool | Punching holes and U-shaped grooves | Ideal for adding additional features to panels |
CCD Vision Recognition Tool | Printed acoustic panels | For precise cutting of printed patterns |

4. Software and Machine Setup
Intelligent Nesting Software
A good CNC machine will come with smart software that helps optimize your cutting layout. This means you can reduce material waste and improve efficiency. It’s all about getting the most out of your materials while cutting costs!
User-Friendly Operation
Look for a machine with intuitive software and controls. A user-friendly interface means your operators can spend less time figuring out how to use the machine and more time actually cutting. It’s all about making your life easier!
5. Conclusion: The Final Verdict
To sum it up, when choosing a cutting machine for acoustic panels, consider material compatibility, precision, cutting speed, flexibility, and ease of operation. The CNC oscillating knife cutting machine is the clear winner in all these categories. With its speed, precision, eco-friendliness, and adaptability, it’s the best solution for cutting acoustic panels.
So, if you’re ready to take your acoustic panel production to the next level, a CNC oscillating knife cutting machine is your best bet. Trust me, it’ll make your life a whole lot easier—and your panels will thank you for it!