When it comes to manufacturing gaskets, the choice of cutting technology plays a pivotal role in determining the quality, efficiency, and versatility of production. As an engineer at AMOR CNC, I’ve seen firsthand how the right CNC oscillating knife cutting machine can make all the difference.
Key Factors in Selecting a CNC Oscillating Knife Cutting Machine
Selecting the best CNC oscillating knife cutting machine for gaskets boils down to a few critical factors: precision, stability, material versatility, and tool adaptability. Let’s dive into why these are crucial.
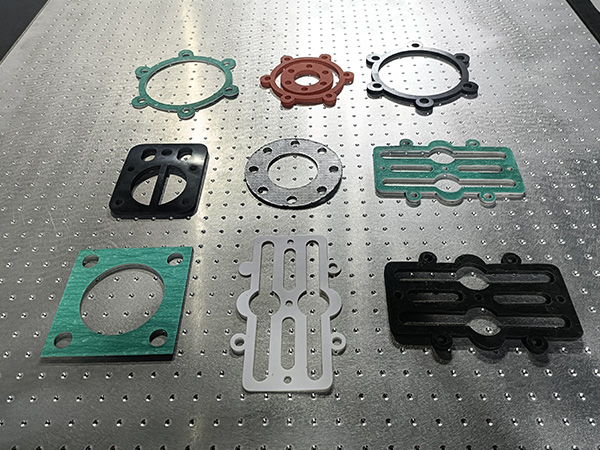
Why Precision and Stability Matter
Precision and stability are not just buzzwords; they are the foundation of high-quality gasket production. A machine that offers high precision for continuous and stable cutting ensures that each gasket is cut to exact specifications, reducing waste and improving product quality.
Material Versatility: A Must for Gasket Manufacturing
Gaskets are made from a wide range of materials, each with its own cutting requirements. A versatile CNC machine can handle everything from rubber and asbestos to graphite reinforcement and epoxy resin board, making it a valuable asset in gasket manufacturing.
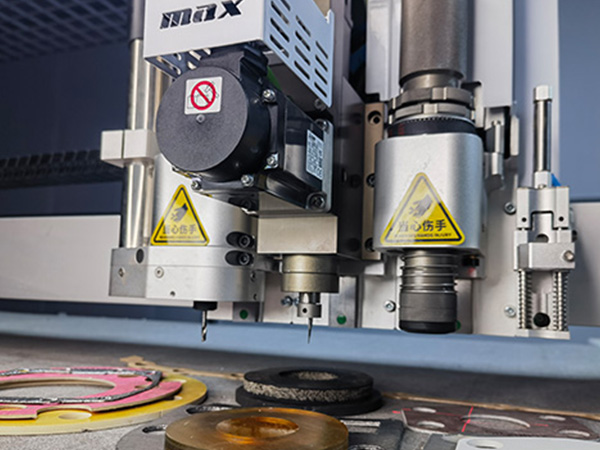
Tool Adaptability and Customization
The ability to customize tools and settings for different materials is essential. This flexibility ensures that whether you’re cutting soft silicone boards or hard Teflon boards, you achieve clean, precise cuts every time.
At AMOR CNC, we’ve engineered our CNC oscillating knife cutting machines to meet these critical needs. Our machines are designed with precision, stability, material versatility, and tool adaptability in mind, making them the ideal choice for gasket manufacturing.
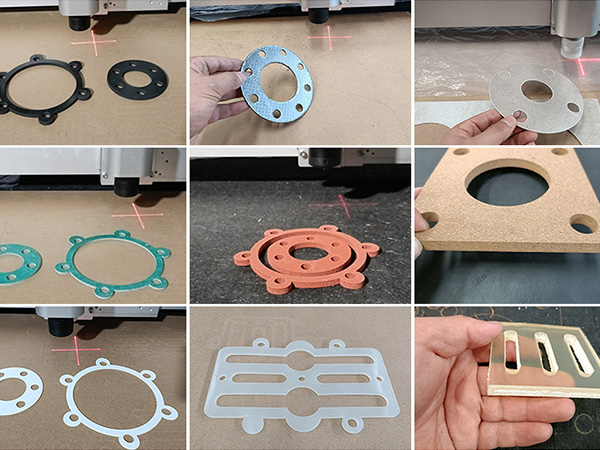
Our Machine’s Precision and Stability
Our heavy-duty integral welding bed and scientific driven design, featuring dual Mitsubishi servo motors and a precision reducer, ensure minimal vibration during rapid cutting. This design philosophy extends to our high-quality transmission system, which uses Taiwan HWIN silver guide rails and a 1.5 tooth mold grinding rack, ensuring high-precision cutting.
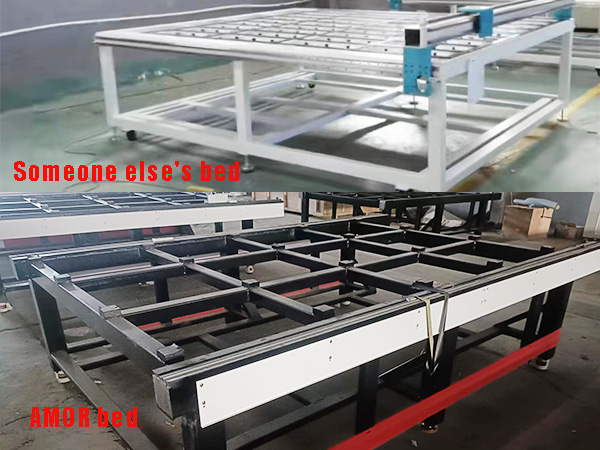
Material Versatility with Our Machine
Our machines are capable of handling a diverse range of materials used in gasket production. From rubber and asbestos to the more challenging carbon fiber and glass fiber cloth, our machines cut with precision and efficiency.
Customization and Tool Adaptability
We offer a variety of cutting tools, including high-power 400W integrated oscillating cutting tools for hard materials and pneumatic oscillation for softer materials. Our tool holder system is designed to minimize the Z-axis gap, ensuring high-precision cutting across all materials.
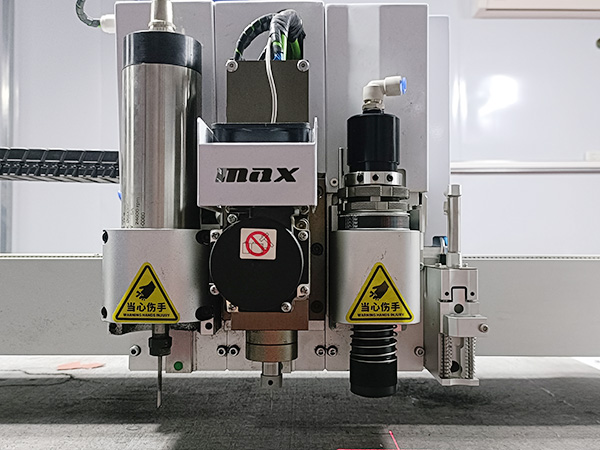
Our clients, from industries ranging from automotive to aerospace, have seen significant improvements in their gasket production processes. Our machines have not only increased production efficiency but also significantly reduced material waste, contributing to a more sustainable manufacturing process.
Conclusion
Choosing the right CNC oscillating knife cutting machine for gasket production is a decision that impacts every aspect of your manufacturing process. At AMOR CNC, we’ve dedicated ourselves to designing and building machines that meet the high standards of precision, stability, material versatility, and tool adaptability required for top-tier gasket production. With our machines, you’re not just investing in technology; you’re investing in the future of your manufacturing process.
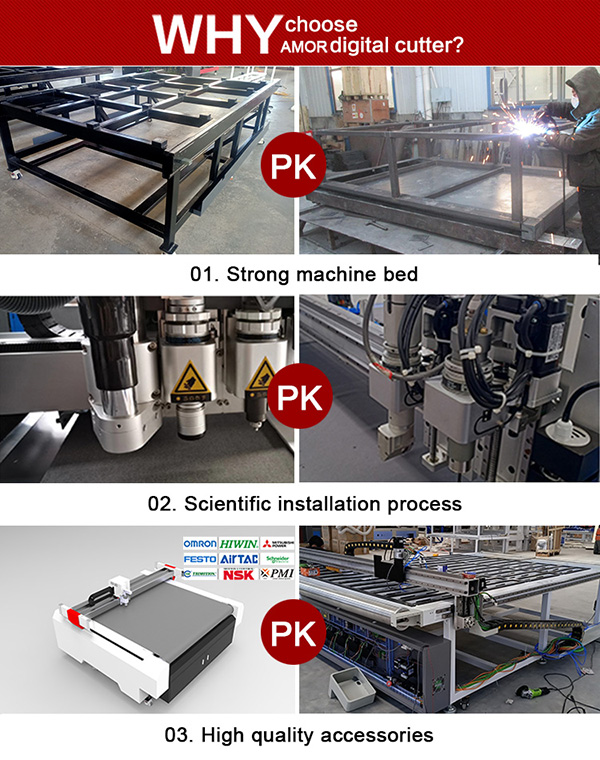
In the world of gasket manufacturing, settling for anything less than the best is not an option. With AMOR CNC’s oscillating knife cutting machines, you’re choosing a partner committed to excellence and innovation in every cut.