Breaking the Design Limitations: How AMOR Oscillating Knife Cutting Machine is Revolutionizing the Polyester Fiber Acoustic Panel Industry
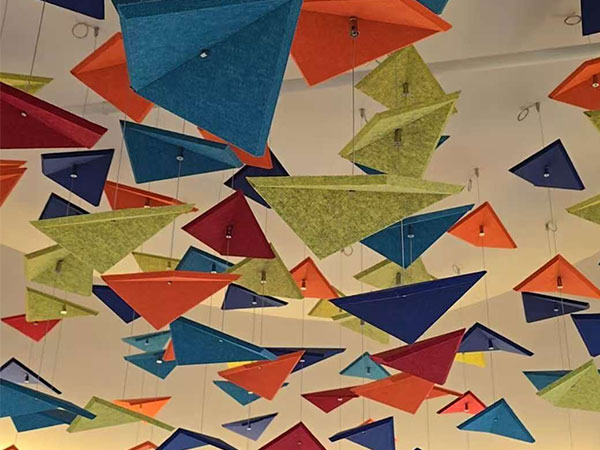
This article showcases how AMOR CNC’s oscillating knife cutting machines break the design limitations in the polyester fiber sound-absorbing panel industry. From versatile tool configurations to years of experience and intelligent software, AMOR CNC offers a complete solution that helps customers achieve complex designs with ease. The article walks through a customer’s journey of disbelief to joy, highlighting the flexibility of our machines in handling various cutting and grooving needs. By the end, you’ll see how AMOR CNC can help you turn your wildest design ideas into reality.
Training Process at a Phenolic Foam Duct Production Facility in Dubai: A Journey with AMOR CNC
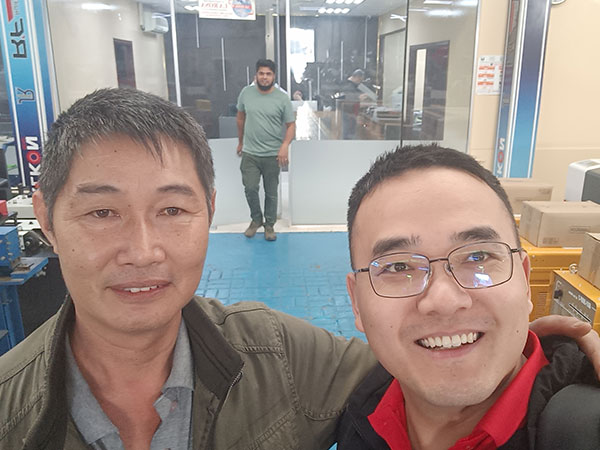
As an after-sales engineer for AMOR CNC, I recently had the opportunity to visit a client’s phenolic foam duct manufacturing facility in Dubai. The experience provided valuable insights into both the machine training process and the unique requirements of producing phenolic foam ducts. In this article, I’ll share the training journey, the reasons the client chose AMOR CNC, and some key lessons learned that can help others in the industry when selecting and operating a cutting machine.
CNC Gasket Cutting Machine vs. Traditional Machining Compared
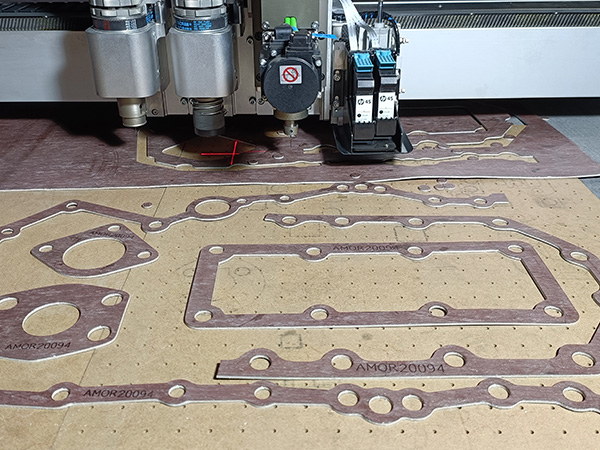
In manufacturing, precision and efficiency are key drivers of success. This article explores the differences, benefits, and applications of CNC gasket cutting machines and traditional methods, helping you choose the best solution for your production needs.
Key Lessons from a Hands-On Training Experience with AMOR CNC Oscillating Knife Cutting Machines
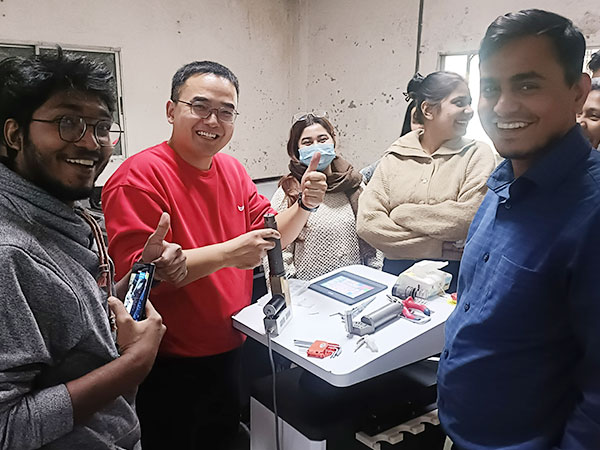
In December 2024, I had the opportunity to provide on-site training in Bangladesh for a polyester fiber sound-absorbing panel cutting machine equipped with a dual-tool holder. This machine utilized an electric oscillating cutting tool and a bevel cutting tool, enabling simultaneous cutting and grooving processes. The training went smoothly, thanks to the customer’s enthusiasm and preparedness. Reflecting on this experience, I want to share some insights to help other customers effectively install, operate, and learn their machines.
Difference Between CNC Knife Cutter Machines and CNC Router Machines

Both CNC Knife Cutter Machines and CNC Router Machines are advanced, automated tools used for cutting materials with high precision. However, they are designed for different types of materials and cutting processes. Here’s a detailed comparison of the two:
5 Common Mistakes Customers Make When Choosing an Oscillating Knife Cutting Machine
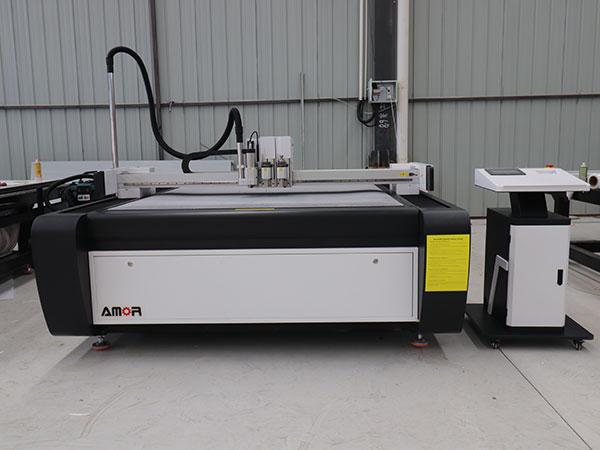
Choosing the right oscillating knife cutting machine for your production needs is crucial to ensure efficiency, precision, and cost-effectiveness. Many customers, however, make certain common mistakes in their decision-making process, often due to misconceptions or a focus on features that are not aligned with their actual production requirements. In this article, we will outline these common mistakes and provide expert guidance on how to avoid them.
Advanced Techniques for Manufacturing Pre-Insulated Phenolic Ducts
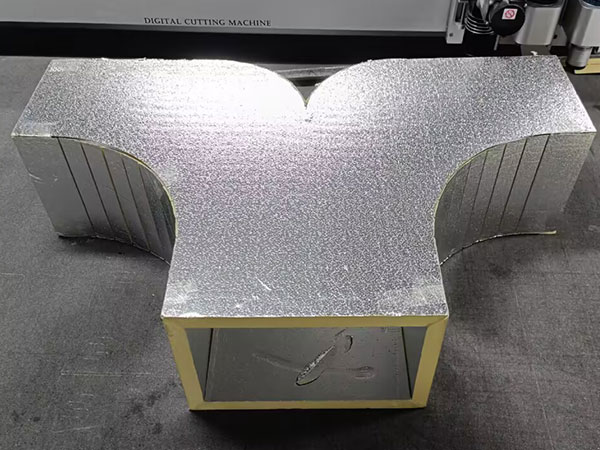
Phenolic ducts are essential components in HVAC systems, widely used in commercial, public, and industrial buildings. Their lightweight structure, excellent insulation, and durability make them a preferred choice over traditional galvanized steel and fiberglass ducts. In this article, we explore the comprehensive process of manufacturing pre-insulated phenolic ducts, comparing manual and automated methods while highlighting the advantages of using a Pre-Insulated Duct Cutting Machine.
CNC Foam Cutting Machines for Packaging Inserts: Comprehensive Guide

From understanding the types of foam cutting machines to practical tips on installation, operation, and maintenance, this article is designed to help businesses maximize the potential of oscillating knife technology for efficient, cost-effective, and versatile foam cutting solutions.
Polyester Fiber Acoustic Panel Cutting Machine: Everything You Need to Know

Are you looking to grow your profits and stand out in the competitive acoustic decoration market? Not sure if a polyester fiber sound-absorbing panel cutting machine is the right choice for your business? This guide is here to help.
Everything You Need to Know About AMOR CNC Oscillating Knife Cutting Machines
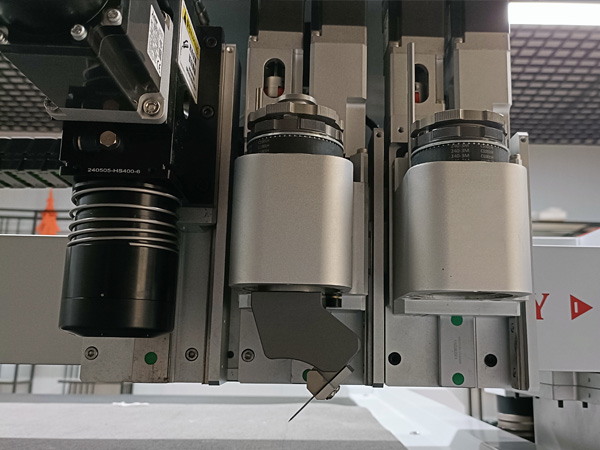
Choosing the right cutting machine for your production needs can feel overwhelming. That’s why we’ve broken down everything you need to know about AMOR CNC oscillating knife cutting machines into an easy-to-follow Q&A format. Whether you’re new to oscillating knife technology or considering upgrading, this guide will answer all your questions.