Why Precision Matters in PTFE Gasket Cutting?
Why is precision so important when it comes to cutting PTFE gaskets? Well, let me explain. PTFE is a tricky material. Its chemical resistance, temperature durability, and non-stick properties make it an ideal choice, but also challenging to cut. Traditional methods like die cutting just don’t provide the level of accuracy needed.
If your gaskets aren’t cut to exact specifications, they won’t seal properly, and in industries like chemical processing, that could spell disaster. Precision is key. Even the smallest deviation can lead to failure in high-pressure environments. That’s why I always recommend CNC PTFE gasket cutting machines.
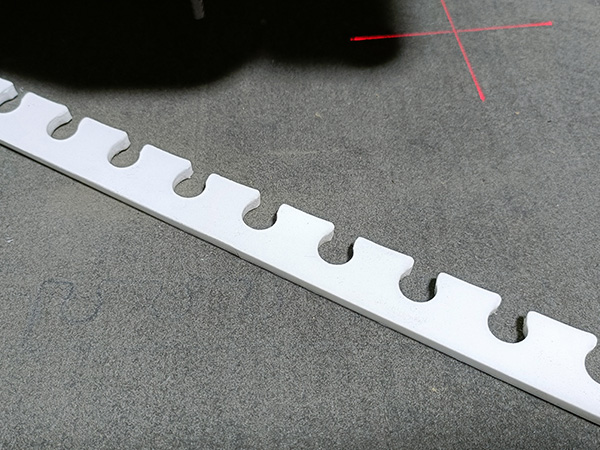
How Does a PTFE Gasket Cutting Machine Work?
So, how does this magical machine work? In short, a CNC (Computer Numerical Control) PTFE gasket cutting machine uses pre-programmed designs to cut gaskets from PTFE sheets with absolute precision. The machine moves its cutting tool along the material, following exact coordinates input via software.
Most of the time, we use oscillating knife cutters for PTFE because they’re designed for non-metallic materials. These cutters slice through PTFE sheets like butter, ensuring clean edges without any of that annoying burr or roughness you get with less precise tools.
What Are the Key Features of a PTFE Gasket Cutting Machine?
At this point, you’re probably wondering what makes a PTFE gasket cutting machine stand out. Here’s a quick rundown of its key features:
- High Precision Cutting: Accuracy is everything in gasket production, and this machine delivers. The cutting precision can reach up to 0.1mm, which means your gaskets will always meet exact specifications.
- Customizability: You can easily program custom designs without needing to create a new die, saving you both time and money.
- Material Efficiency: By optimizing the cutting path, these machines minimize waste. Who doesn’t want to save on material costs?
Oh, and let’s not forget the fact that there’s no need for dies. With traditional methods, you had to create a new die for each design, which was time-consuming and costly. A CNC cutting machine takes care of that.

Why Should You Invest in a PTFE Gasket Cutting Machine?
Now, you might be thinking, “Why should I invest in this machine? I’ve been doing fine with my old methods.” Well, let me tell you – once you start using a CNC PTFE gasket cutting machine, there’s no going back.
The first thing you’ll notice is how much faster it is. You can cut custom gaskets in minutes, not days. This is crucial if you’re handling large orders with tight deadlines. Plus, the accuracy ensures that there’s almost no waste, saving you money on materials.
With CNC cutting machines, you also have the flexibility to work with a wide range of materials, not just PTFE. Rubber, silicone, and non-asbestos gaskets are just a few examples of what these machines can handle. This versatility makes it a smart investment if you serve multiple industries.
Comparing Traditional Methods vs. CNC PTFE Gasket Cutting Machines
Let’s talk about traditional methods for a minute. Sure, die cutting or even laser cutting might get the job done, but they have significant limitations. Die cutting requires expensive molds, which need to be changed for every design. Laser cutting, on the other hand, can leave burnt edges on PTFE, compromising the gasket’s integrity.
With a CNC PTFE gasket cutting machine, you avoid all these pitfalls. There’s no need to create new molds, and the oscillating knife cuts clean, accurate edges without heat or material damage.

Conclusion: Making the Right Investment in PTFE Gasket Cutting
In today’s fast-paced manufacturing world, precision, speed, and efficiency are critical. A CNC PTFE gasket cutting machine offers all of this and more. With features that ensure high precision and material efficiency, this machine is a must-have for businesses looking to stay ahead in gasket production.
So, is it time to upgrade your process? Absolutely. Your clients—and your bottom line—will thank you.