Challenges with Traditional Genuine Leather Cutting Methods
- High Material Waste
Traditional leather cutting methods are often manual, relying on skilled craftsmen to cut leather pieces. Due to the irregular shapes and defects inherent in natural leather hides, this manual process frequently results in significant material waste. Craftsmen must carefully avoid defects, leading to inefficient use of the leather. - Low Efficiency
Manual cutting is time-consuming. Each hide must be carefully inspected, marked for defects, and cut by hand, which slows down the production process. This inefficiency can lead to longer lead times and higher costs, making it challenging to meet high demand and tight deadlines. - High Labor Costs
Skilled craftsmen are essential for manual leather cutting, but they come with high labor costs. The expertise required to accurately cut irregular leather pieces while minimizing waste is not easily found, and experienced workers demand higher wages. - Recruitment Difficulties
Finding skilled craftsmen is increasingly difficult. Younger generations are less inclined to pursue careers in manual craftsmanship, leading to a shrinking pool of qualified workers. This scarcity of skilled labor further exacerbates the high costs and inefficiencies associated with traditional leather cutting methods.

Intelligent Cutting Solutions: CNC Oscillating Knife Cutting Machines
- Marking Leather Defects
To overcome the challenges of manual cutting, the first step in the intelligent cutting process is to identify and mark defects on the leather. This pre-processing step ensures that the cutting process can proceed efficiently without compromising the quality of the leather. - Vision Recognition System
A vision recognition system is integral to the CNC oscillating knife cutting machine. This system performs several crucial functions:
Defect Identification: Accurately detects and maps the marked defects on the leather hide.
Contour Detection: Recognizes the irregular contours of the leather hide, allowing for precise planning of the cutting process. - Intelligent Nesting Software
The identified defects and contours are then processed by intelligent nesting software, which optimizes the placement of cut pieces to maximize material usage and minimize waste. Key features of the nesting software include:

Automatic Nesting: Automatically arranges cutting patterns within the usable areas of the leather, considering its irregular shape and defects.
Customizable Nesting: Allows customers to specify particular cut pieces for different areas of the leather based on thickness variations, ensuring optimal use of different sections of a single hide.
Multi-Hide Nesting: Can simultaneously nest patterns across multiple irregular leather hides, enhancing efficiency and precision.

Benefits of Intelligent Cutting Technologies
Enhanced Precision and Quality
The combination of vision recognition and intelligent nesting software ensures that each cut is precise and avoids defects. This results in higher-quality finished products with consistent standards.
Improved Material Utilization
Optimizing the placement of cut pieces significantly reduces material waste, leading to lower production costs and more sustainable manufacturing practices.
Increased Efficiency
Automation reduces the need for manual intervention, speeding up production times and increasing overall efficiency. This allows manufacturers to meet tight deadlines and handle large orders effectively.

Customization and Flexibility
Manufacturers can easily customize cutting patterns and adapt to specific customer requirements. The ability to differentiate between various sections of the leather hide based on thickness and quality further enhances product customization.
Reduced Labor Costs and Recruitment Challenges
By reducing the reliance on skilled craftsmen, CNC oscillating knife cutting machines help lower labor costs and mitigate the difficulties associated with recruiting skilled workers. Automation ensures that the cutting process remains efficient and precise, even with fewer manual labor inputs.
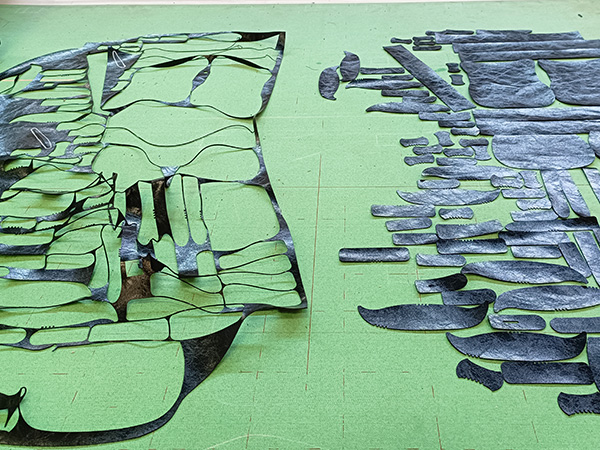
Application in the Sofa and Automotive Interior Industry
Sofa Manufacturing
In sofa manufacturing, precise cutting of irregular leather ensures that each piece fits perfectly, contributing to the overall aesthetic and comfort of the final product. The flexibility to create customized designs helps manufacturers cater to diverse consumer preferences while improving efficiency and reducing costs.
Automotive Interiors
For automotive interiors, where precision is paramount, CNC oscillating knife cutting machines ensure that each leather piece meets stringent quality standards. This is crucial for maintaining the high-end look and feel of luxury vehicles, as well as ensuring the durability and functionality of interior components.

Conclusion
The integration of CNC oscillating knife-cutting machines with vision recognition systems and intelligent nesting software has transformed the cutting of irregular leather materials in the sofa and automotive interior industry. These technologies address the challenges of traditional cutting methods, such as high material waste, low efficiency, high labor costs, and recruitment difficulties.
Manufacturers can achieve superior product quality, reduced production costs, and enhanced customization capabilities by enabling precise, efficient, and intelligent cutting solutions. Embracing these intelligent leather cutting solutions is essential for staying competitive and meeting the growing demand for high-quality, customized leather products.