In today’s market, meeting personalized customer demands is the key to success. To boost efficiency, cut costs, and deliver high-quality custom products, choosing the right tools is essential.
This guide covers everything you need to know about cutting polyester fiber panels, from the benefits of oscillating knife machines to tips on choosing the right manufacturer and using the machine effectively. Whether you’re new or experienced in the industry, this resource will help you make smarter decisions and grow your business.
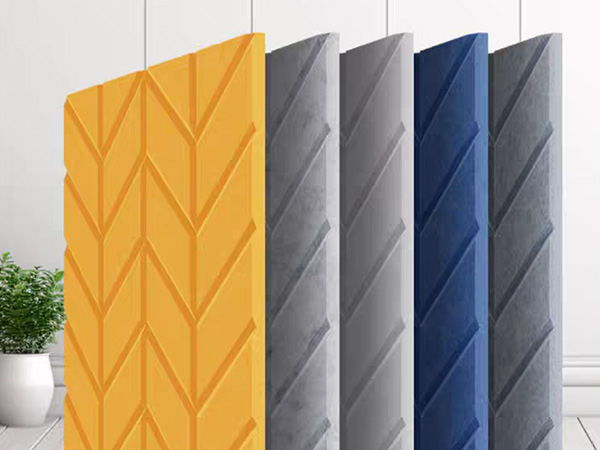
Part 1: How to Create Acoustic Panel Decorative Products
What Are Polyester Fiber Sound-Absorbing Panels?
Polyester fiber sound-absorbing panels are lightweight, durable, and versatile materials used in acoustic treatment. Made from compressed polyester fibers, they effectively reduce noise and reverberation in spaces.
What Decorative Products Can Be Made from Them?
- Wall and ceiling panels
- 3D acoustic decorations
- Lampshades
- Partition screens
- Artistic soundproofing elements
How Are Polyester Fiber Sound-Absorbing Products Made?
The production process includes cutting and grooving the panels into specific shapes and designs. Advanced cutting equipment ensures high precision and efficiency, making it easy to meet diverse design requirements.
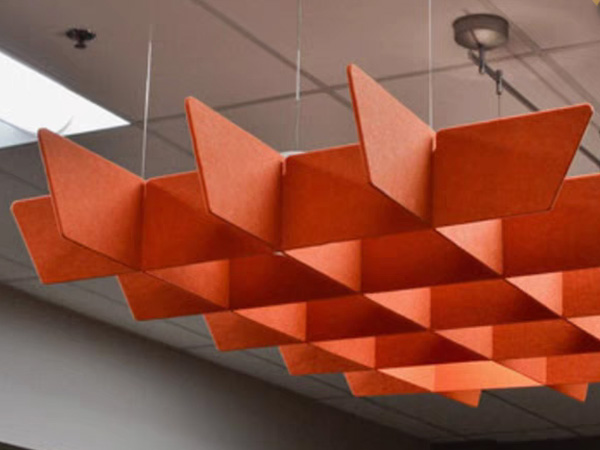
Part 2: Common Production Techniques for Polyester Fiber Acoustic Products
Advantages and Disadvantages of Manual Production
Advantages: Low initial investment, suitable for simple tasks.
Disadvantages: Low efficiency, inconsistent results, and high reliance on skilled labor.
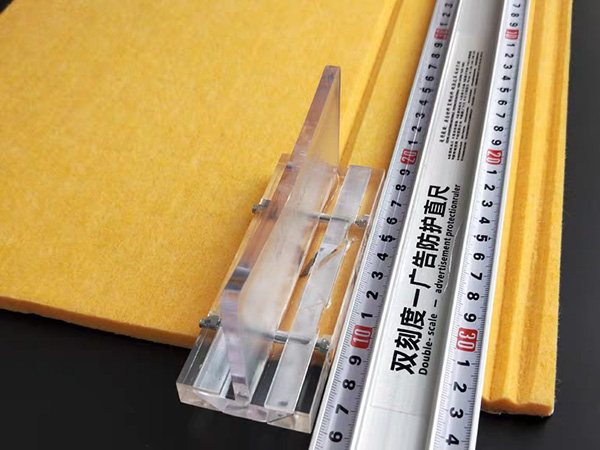
Why Is Laser Cutting Not Ideal for Polyester Fiber Panels?
Laser cutting generates heat, which can:
- Burn or melt the material.
- Produce smoke and odors.
- Result in uneven or hardened edges.
Importance of Meeting Design Requirements
Modern designs require intricate shapes, complex grooves, and 3D effects. Traditional cutting methods often fail to meet these demands, leading to serious market losses.
To stay competitive, meeting design needs is essential. Investing in advanced cutting technology ensures you keep clients, grow profits, and stay ahead in the market.

A Better Equipment Solution: Oscillating Knife Cutting Machine
What Is an Oscillating Knife Cutting Machine?
A CNC machine that uses oscillating blades to perform cold, precise cutting without damaging materials.
Benefits of Using Oscillating Knife Cutting Machines
- High efficiency and precision.
- Dust-free and environmentally friendly process.
- Suitable for complex designs and diverse thicknesses.
- Reduces labor dependency and enhances production quality.

Part 3: Polyester Fiber Sound-Absorbing Panel Cutting Machine
Features and Advantages
- High-speed cutting (300–400mm/s).
- Clean edges with no material damage.
- Easy-to-use software for customization.
- Support for V-grooving, straight cuts, and curved designs.
Types
- Single-head oscillating knife machines.
- Dual-head machines for simultaneous cutting and grooving.
- With CCD recognition system can meet the precise cutting of the pattern outline of the printed acoustic boar.
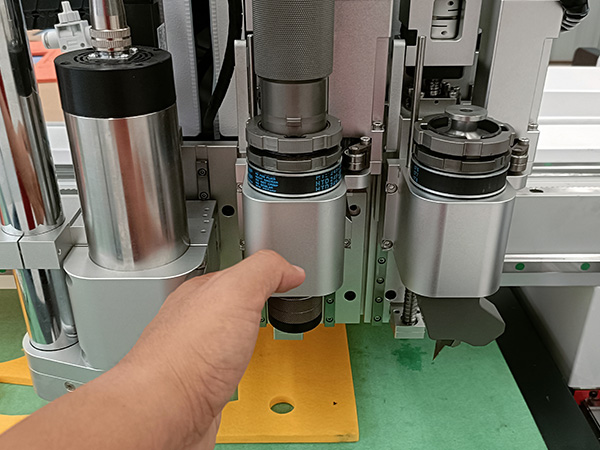
Specifications
- Cutting Thickness: 9mm to 50mm.
- Bevel Angles: 5°, 10°, 15°, 22.5°, 30°, and 45°.
- Processing Area: Standard size is 1600mm x 2500mm, with customizable options available to match the dimensions of your panels.
MODEL | AMOR-1610 | AMOR-1625/30/40 | ACCEPTING CUSTOMIZATION |
---|---|---|---|
Effective Working Area | 1600X1000mm | 1600X2500/3000/4000mm | |
Total Measurement Y/X/Z | 2180X1610X1250mm | 2180X3200/3700/4700X1250mm | |
Type of Work Platform | MK series: fixed table; BK series: automatic feeding table | ||
Multi-Head Optional | Double head optional efficiency doubled, double gantry optional, double head mutual shift optional, length can be customized | ||
Multi-Function Tool | Vibrating knife full cutting, high power active round knife, semi-cutting cutting, full cutting cutting, camera positioning cutting, edge finding cutting, acrylic milling cutter, cursor positioning, line marking, indentation knife, V-groove knife, etc. | ||
Safety Devices | Infrared sensing, safe and reliable | ||
Cutting Speed | 0-2000mm/s | ||
Cutting Thickness | ≤50mm Other thicknesses can be customized according to the material | ||
Transmission Port | Network port | ||
Material Fixing Method | Vacuum partition adsorption | ||
Transmission System | Mitsubishi servo motor + high precision helical gear reducer + 1.5m grinding rack + HWIN guide rail | ||
Rated Power | 11kw | ||
Rated Voltage | 380V±10%/220V±10%(A suitable transformer can be configured according to the customer’s local voltage) | ||
Control System | LCD touch screen, support Chinese, English, Italian, Spanish, Russian, Korean | ||
Software | Automatic nesting software, camera positioning, large format camera system | ||
Support File Format | AI、PLT、DXF、CDR etc. |
Part 4: Manufacturers and Suppliers
Top 6 Cutting Machine Manufacturers
AMOR CNC
- Specializes in oscillating knife cutting machines.
- Ideal for polyester fiber acoustic panels with high precision and efficiency.
- Strong in producing intricate designs and custom grooves.
Zünd
- Known for modular digital cutting systems.
- Offers customizable machines for various industries.
- Focuses on automation and large-scale efficiency.
Esko
- Provides cutting tables for packaging and printing.
- Combines cutting technology with design software for seamless workflows.
- Excellent for prototyping and short-run production.
Summa
- Offers vinyl cutters and flatbed systems.
- Known for user-friendly, durable machines.
- Serves signage, textiles, and packaging industries.
Atom
- Specializes in cutting leather, textiles, and composites.
- Trusted for automotive, footwear, and fashion industries.
- Machines are robust and adaptable.
Aristo
- Focuses on large-format cutting solutions.
- Handles plastics, textiles, and composites effectively.
- Strong in signage, packaging, and aerospace applications.

How to Find a Reliable Manufacturer
- Check Their Website
See if they offer machines specifically recommended for polyester fiber sound-absorbing panels. - Search Online Platforms
Look for their presence on Alibaba, Google, or YouTube. A strong online presence shows credibility and product availability. - Request a Cutting Sample
Visit their facility for a demonstration to confirm they have experience in your industry. - Evaluate After-Sales Support
Ensure they provide training, technical support, and readily available spare parts. - Look for Success Stories
Check if they have case studies or examples of successfully working with similar businesses.

How to Contact Manufacturers
Once you have found a business that makes oscillating knife cutters, the easiest way to contact them is to call or email them. Before calling or emailing, make sure you have the necessary information ready.
● Your contact details and company name.
● A summary of the project you are working on.
● An estimated project schedule
● Project scope and other information.
Get an idea of how much your project will cost. You can also use social media to contact them. If you take this action, use the details listed.

How to Buy A Polyester Fiber Acoustic Panel Cutting Machine
Polyester fiber acoustic panel cutting machines are key to making acoustic panel products. Here are some tips on how to buy a CNC cutting machine.
Understand your processing requirements. Consider the efficiency and cutting needs you want to meet (size, thickness, speed)
Decide on the amount you want to spend.
Find a reputable supplier. Check their website pages, Youtube, and platforms such as Alibaba.
Check if the manufacturer provides proofing testing services
Evaluate their quality standards
Conduct background checks on suppliers
Check if they provide after-sales service
If they provide detailed installation and operation tutorials
If they provide warranty
Place an order and pay
Call to confirm
If detailed testing services are provided before shipment
Check the arrival time
Perform a final inspection after receiving the goods
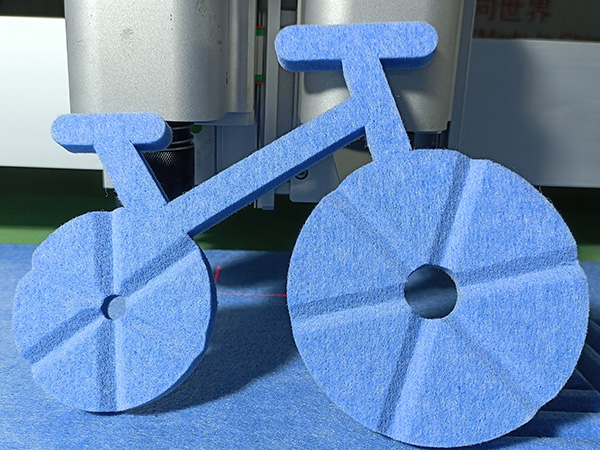
Part 5: How to Choose the Right Cutting Machine
01. Material Compatibility
Ensure the machine supports the thickness, density, and type of polyester fiber panels you need to cut.
02. Tool Configuration
Choose a machine equipped with essential tools like oscillating knives and bevel cutters for diverse cutting and grooving needs.
03. Cutting Efficiency and Precision
Look for a machine with high cutting speed and consistent accuracy, especially for intricate designs and complex grooves.
04. Customization and Flexibility
Confirm whether the machine’s cutting area or tool setup can be customized to fit your specific production requirements.
05. Ease of Use
Opt for machines with user-friendly software and simple operations to save on training time and improve productivity.
06. After-Sales Support
Ensure the manufacturer provides strong technical support, spare parts availability, and clear warranty terms.
07. Cost and Manufacturer Reputation
Select a machine that offers good value for money, backed by a trusted supplier with positive reviews and relevant industry experience.

Part 6: How to Install an Oscillating Knife Cutting Machine
Installation Space
For a machine with a 1600mm x 2500mm cutting area, ensure a space of at least 3000mm x 4000mm.
This allows room for auxiliary parts, material loading/unloading, and operator movement.
Electrical Requirements
Voltage: Requires 380V (three-phase) or 220V (single-phase).
If your local voltage differs, use a voltage converter or frequency converter to protect electrical components.
Air Switch: For 380V, use a 45A air switch.
Cables: Use 4mm² copper wires to ensure stable power during operation.
Assembling the Machine
Set up the frame and cutting table according to instructions.
Attach necessary parts like vacuum pumps or air compressors securely.
Control System Setup
Install the provided software on your computer.
Connect the machine via cable or network for operation.
Calibration
Adjust cutting depth, speed, and alignment for your material.
Test with sample cuts to ensure accuracy.
Operator Training
Train staff on software usage, tool setup, and safety measures.
Final Testing
Run a trial with production materials and adjust settings as needed before starting regular operations.
This simple setup ensures reliable performance and smooth operation.
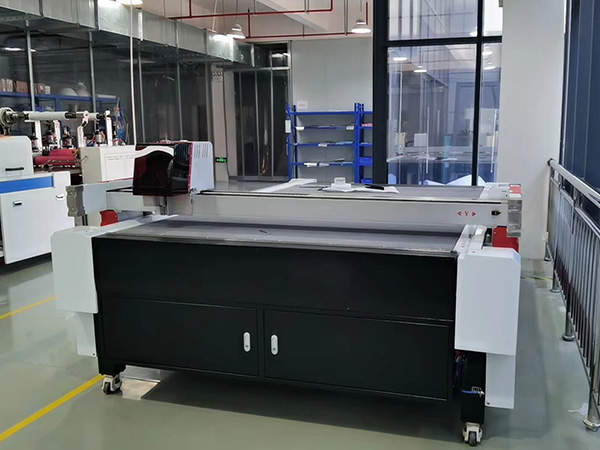
Part 7: Essential Accessories for Oscillating Knife Cutting Machines
Blades
- The primary cutting tools; replace them regularly to ensure clean and precise cuts.
Table Mats
- Protect the cutting table and provide a stable surface for materials during cutting.
Spare Tools
- Backup tools like additional blades or cutting heads to avoid downtime during production.
Belts and Limit Switches
- Critical for the machine’s movement and positioning; keep spares to maintain smooth operation.
Backup Screws and Small Parts
- Essential for quick repairs or replacements of minor machine components.
Installation Tools
- Tools like wrenches and screwdrivers for setting up and maintaining the machine.
Guide Rail Sliders
- Ensure smooth motion of the cutting head; inspect and replace as needed to maintain precision.

Part 8: How to Operate a Polyester Fiber Cutting Machine
- Learn the Installation Tutorial
- Follow the manufacturer’s video and text guides to install the machine step by step.
- Optimize the Software
- Master the design software to maximize material usage, set cutting sequences, SP operation numbers, and directions for precise, efficient cuts.
- Install Tools Correctly
- Ensure blades and tools are firmly installed. When the W-axis data is 0, the blade should point toward the machine’s X+ direction for accurate cutting.
- Set Cutting Depth and Speed
- Adjust blade depth to match the material thickness, ensuring full penetration without damaging the workbench surface.
- Stay Connected for Support
- Contact the manufacturer for quick troubleshooting or technical assistance when needed.

Part 9: Tips for Cutting Machine Maintenance
Daily Maintenance
- Clean the cutting table and tools daily with a high-pressure air gun to remove waste and debris.
- Regularly check the belt and blade for wear and replace if needed.
Key Maintenance Tips
- Store spare parts in a dry, clean place.
- Use compressed air to clean machine components.
Safety Precautions
- Never touch the blade during operation.
- Regularly inspect electrical connections to ensure safety.
Weekly Maintenance
- Lubricate the X/Y/Z axis guide rails and racks weekly using appropriate lubricant and grease to maintain smooth operation and prevent wear.
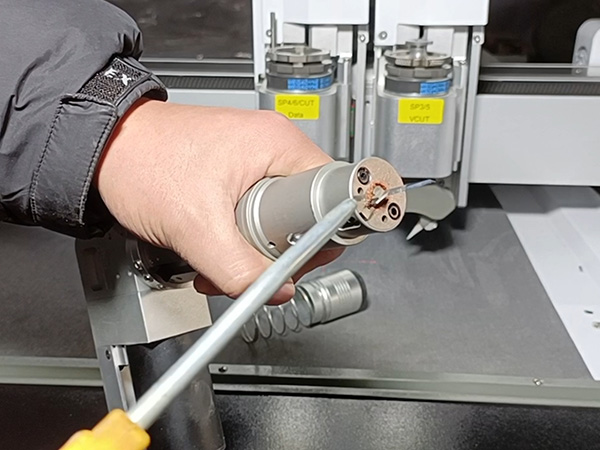
Conclusion
A polyester fiber sound-absorbing panel cutting machine is an essential tool for producing high-quality acoustic and decorative products. With the right machine, tools, and maintenance practices, you can achieve efficient and precise results, making it a valuable investment for your business.