Let’s Get to Know the Blade First
Oscillating knife blades typically have four main parts:
Part | Description |
---|---|
Handle | 10mm in length, fixed using two set screws inside the blade holder |
Edge | The sharp part; must align with the cutting direction |
Spine | Same thickness as handle, adds rigidity |
Tip | The first point of contact to pierce the material |
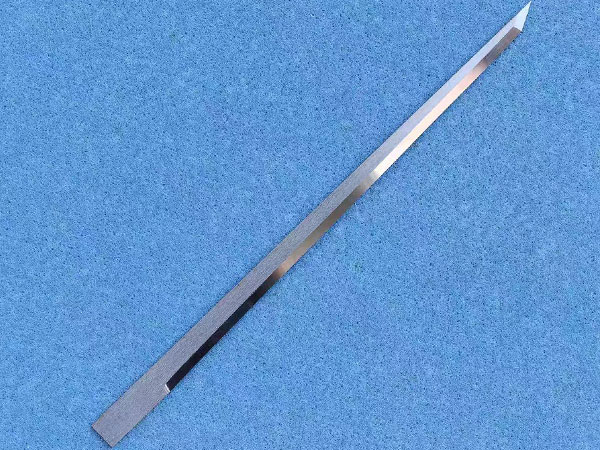
Why Choosing the Right Blade Matters
- ✅ Ensures high-quality cutting results
- 🚫 Prevents machine errors and false alarms
- 💰 Reduces blade wear and lowers long-term costs
A bad blade = lost time, ruined material, and a very grumpy production manager.
Common Types of CNC Gasket Cutting Blades
Blade Thickness
Typically: 0.63mm and 1mm
⚠️ Important: Different blade holders are used depending on thickness. Choose wisely!
Blade Length
Total length: 20–30mm
Effective cutting edge: 8–20mm
Don’t confuse the overall length with the actual sharp edge!
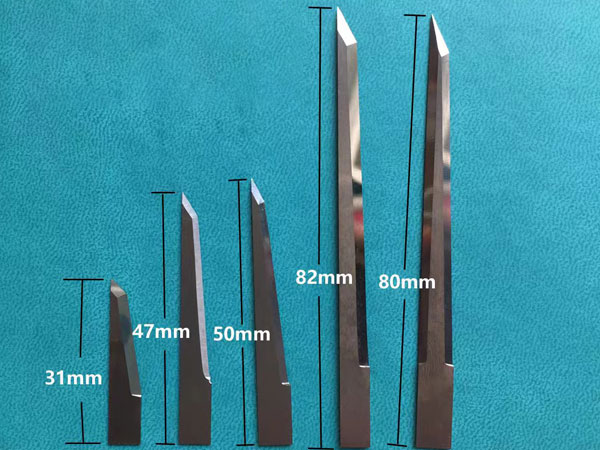
Blade Shape (Angle + Tip)
Blade Angle | Tip Type | Use Case Example |
---|---|---|
16° | Sharp | Small circles, fine cuts |
25° | Sharp | Fragile materials (graphite) |
30°/45° | Flat | Standard cuts |
90° | Flat | Thick rubber (≥10mm) |
Blade Width
- Slanted blades: up to 5mm wide
- Vertical blades: around 2–3mm wide
Blade Material
- Tungsten steel (our standard): hard, durable, long-lasting
- White steel: cheaper, but wears faster
👉 Tungsten steel is what we ship by default – and for good reason.
Does Every CNC Gasket Cutter Need All These Blades?
Nope. Not unless you enjoy wasting money.
Choose based on:
- Material hardness
- Material thickness
- Job requirements (e.g., tiny holes, zero kerf)
Most of our clients settle on 1–3 blade types max, customized for their products.
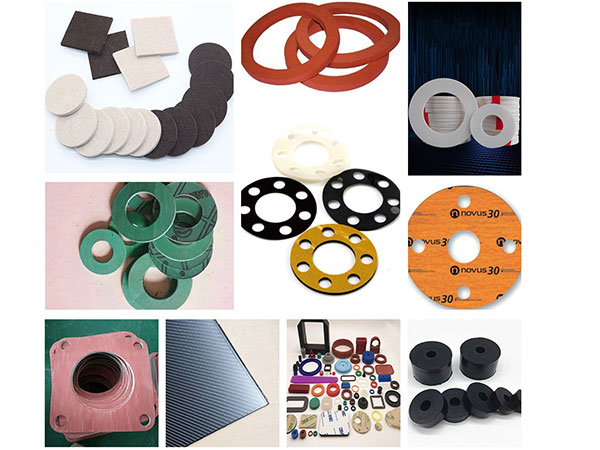
How to Choose the Right Blade? Let Me Show You!
Soft & Thin Gasket Material
Examples: 1–3mm rubber, 0.3–1mm non-asbestos, cork
Blade: 0.63mm thick, 16° sharp tip
Perfect for quick, clean cuts—even for circles <3mm
🔧 Model: AMOR-16°, 0.63mm sharp tip
Fragile & Brittle Materials
Examples: 1–5mm graphite
Blade: 25°, 0.63mm sharp tip
Clean edges, no chipping, no crumbly mess
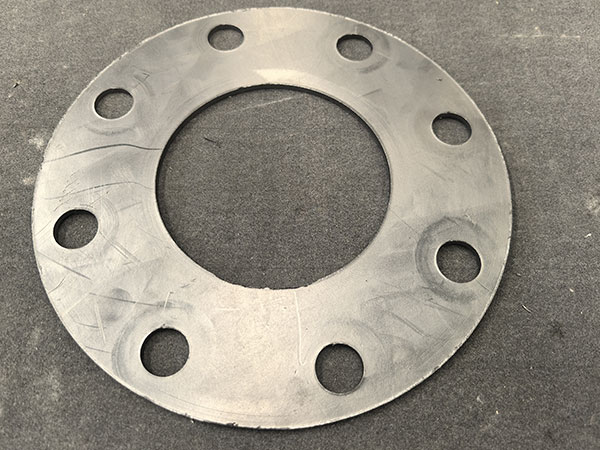
Hard But Thin Materials (<5mm)
Examples: PTFE, non-asbestos
Blade: 16°, 1mm flat tip
Add a 2mm wide, 8mm long vertical blade for tiny circles
Reinforced Gaskets (with steel layer)
Examples: Graphite reinforced with stainless mesh
Blade: 25° flat tip, 10mm edge length
Strong, durable—and less likely to snap

Thick Rubber (10–15mm)
Blade: 90°, vertical edge, 12–25mm long
Smooth cuts for round holes ≥7mm
What Happens When You Pick the Wrong Blade?
Blade Too Short
Can’t pierce the material → ragged edges
Hard materials? Blade breakage + alarms from tool motor friction
Blade Too Long
Snaps easily, especially on hard stuff
May also cut poorly on curves or small holes
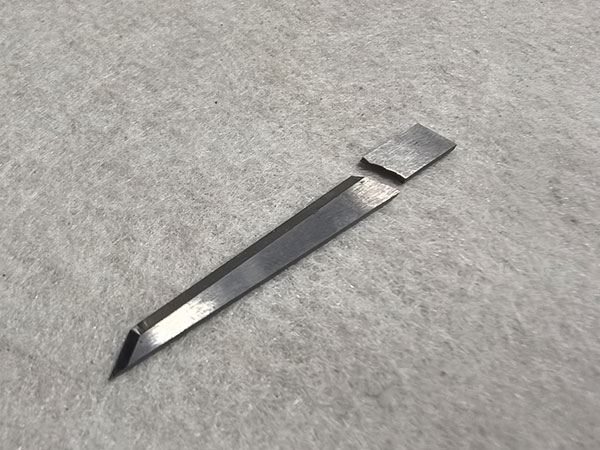
Blade Too Thick
1mm blade + 1.5mm amplitude tool + 2mm rubber = warping
Rubber stretches. Precision drops.
Wrong Tip for Hard Stuff
Using a 16° sharp tip on 2mm PTFE?
Expect one very sad blade tip 😢
How to Choose the Right Blade Length (Yes, It Matters!)
The Formula:
Blade edge length > material thickness + tool amplitude + 2.5mm (safety cap)
But also…
- Cap must lightly press on material
- Spring should be slightly compressed, not maxed out
- If cap floats = blade too long
- If cap squishes too much = overload risk
Examples:
Material Thickness | Tool Type | Tool Amplitude | Ideal Blade Edge Length |
---|---|---|---|
3mm Rubber | Electric Oscillating | 1.5mm | 6–12mm |
3mm Non-asbestos | Pneumatic Oscillating | 9mm avg. | 9–15mm |
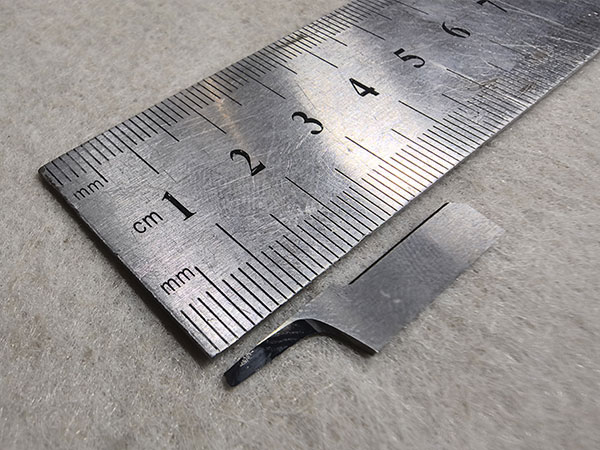
FAQ: Blade Installation, Depth & Usage
How to Install the Blade?
- Make sure tip is centered
- Blade edge must point in cutting direction (X+ when W-axis = 0°)
What’s the Correct Drop Depth?
It’s NOT material-dependent. It’s about blade edge length vs machine zero point.
Should I Buy Extra Blades?
Yes. 1000% yes.
We recommend keeping at least 30 blades on hand at all times.
Blade Keeps Breaking on Hard Gaskets?
Try layered cutting:
Cut 5mm non-asbestos in two passes (2.5mm each).
Faster. Cleaner. Blade lives longer.
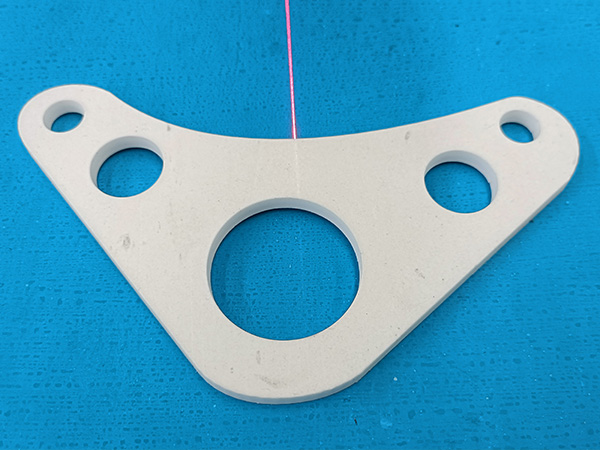
Blade Lifespan?
About 10–15 days, depending on volume and material.
(Unless you’re trying to cut steel with it… don’t.)
Why Is My Cut Edge Fuzzy?
Blade edge is not facing the cutting direction.
Check W-axis = 0°, blade edge = X+.
How Do I Know My Blade Is Dull?
- Cutting sounds louder
- Material stretches
- Cut edge is rough
= Time for a fresh blade!
Conclusion: Choosing the Right Blade Isn’t Optional—it’s Essential
The wrong blade can mess up your job, cost you time, and even damage your machine.
The right blade? It slices clean, keeps your production moving, and makes you look like a gasket-cutting genius.
Remember:
- Match blade to material, thickness, and tool amplitude
- Don’t skimp on quality or quantity
- Learn proper installation to avoid common mistakes
Choosing blades shouldn’t feel like guessing lottery numbers. After reading this guide, you now know how to make smarter, faster, and more cost-effective decisions.
Want help picking the right blade for your job? Just ask me. I’ve snapped enough wrong blades in my career to know what not to do.