Your Machine Needs More Than Good Hardware — It Needs Smart Software Too
When our client in Manila received their new AMOR CNC phenolic duct cutter, the first thing they noticed was the sleek, robust frame and the industrial-grade components. Looks great, right? But good hardware is only half the story.
What really made the difference was the intelligent software that came with it.
I trained their team step-by-step on how to input duct sizes directly into the software — no AutoCAD needed, no rocket science. The software automatically generated cut shapes, nested them smartly on the material, and sent the cutting files straight to the machine. Boom. Done.
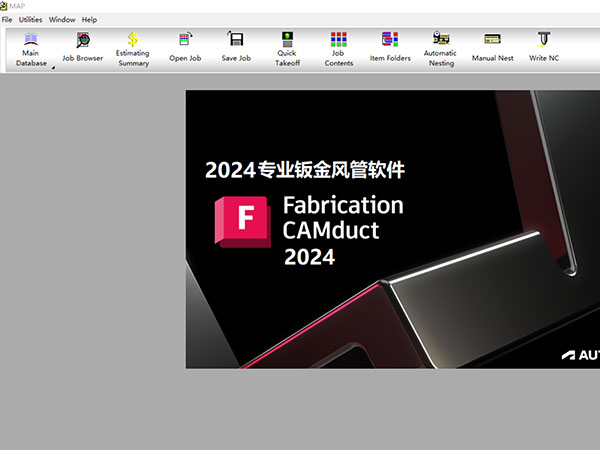
What would’ve taken them hours with manual drawings was completed in minutes.
So, lesson one: Don’t just ask about the machine’s hardware — ask:
- Is there software to automate duct design?
- Can the software handle nesting and output directly to the machine?
- Does the supplier offer training and support?
Without smart software, you’re basically buying a sports car with no steering wheel.
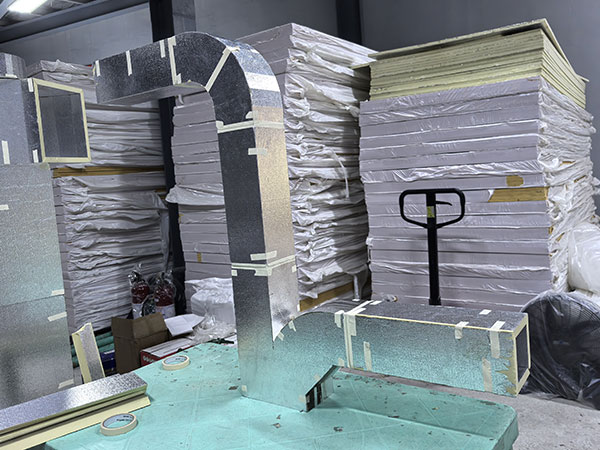
Choose the Right Tools for the Right Duct
You’d think all cutting tools are the same… until your duct corners start looking like pizza slices.
During the Manila installation, I personally guided the client through tool setup—and let me tell you, tool selection is everything when it comes to duct quality.
Here’s the configuration we recommend based on actual use:
- Oscillating Cutting Tool
- Handles vertical straight cuts on phenolic boards.
- Got a stable air compressor (0.6MPA or higher)? → Go for the Pneumatic Oscillating Tool.
- No compressor? → Use the Electric Oscillating Tool with large stroke for similar performance.
- Max cutting speed for phenolic boards? 400mm/s. Exceeding this risks snapping blades. Ask the poor guy who did it mid-demo. (Yes, that happened. We don’t talk about it.)
- Small-Angle Bevel Cutting Tool
- Perfect for grooving curved ducts and elbows.
- Compatible angles: 5°, 7.5°, 10°, 15°, 22.5°.
- 45° Bevel Cutting Tool
- Used for straight duct panels that need slotting and full-depth angled cuts.
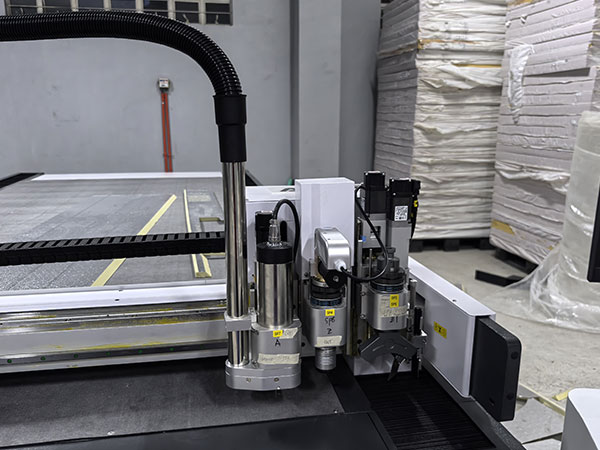
These tools aren’t just nice-to-haves — they’re must-haves. Choosing the wrong one will either slow down your production or wreck your grooves (and your mood).
Don’t Forget Your Spare Blades (Or You’ll Regret It)
Let me tell you a story.
During the training session in Manila, everything was going great… until the client ran out of blades. Midway through cutting a duct set, they turned to me and said:
“Uh, do you have any spares?”
Nope. They hadn’t ordered extra blades.
So, we waited. And by waited, I mean stared awkwardly at the machine for two hours.
Always—ALWAYS—order enough consumable parts when you buy the machine. Especially:
- Cutting blades (get at least 30–50 pcs for a new setup)
- Bevel knife replacements
- Tool holders or springs (depending on usage)
Your machine is only as productive as your spare parts stock. And downtime? That’s just money burning on the shop floor.
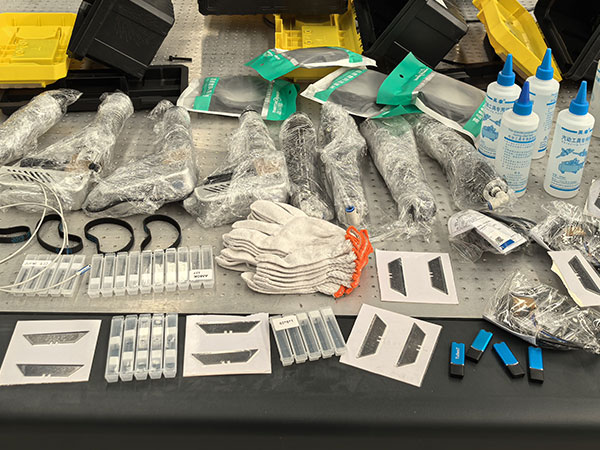
Final Thoughts: Make an Informed Investment
To recap, when choosing a CNC cutting machine for phenolic air ducts, don’t just look at the fancy features or the price tag. Consider:
- ✅ Software capabilities — Can it simplify your duct design and automate workflows?
- ✅ Tool configurations — Do you have the right tools for vertical cuts, small-angle grooves, and 45° bevels?
- ✅ Spare parts — Will you have enough consumables to run production smoothly?
Choosing the right machine isn’t just about specs — it’s about workflow, uptime, and long-term savings.
Our Manila client mastered everything within three days — from blade installation to software operations — and they were producing perfect elbows and straight ducts by day two. That’s the level of support and integration you should expect.
So, before you sign the PO, ask yourself: “Can this machine truly support my production from start to finish?”
If the answer isn’t a solid “Yes,” then it’s time to call us.