Gasket Manufacturing at Precision Seals Inc.
Industry: Gasket Manufacturing
Challenge: Precision Seals Inc. was dealing with high material waste and inconsistent cuts when producing custom gaskets. Their traditional cutting methods just couldn’t keep up with the complexity and precision required.
Solution: We introduced them to our CNC gasket cutting machine, specifically designed for non-metallic materials like rubber and graphite. The machine’s precision allowed them to produce gaskets with tight tolerances, ensuring a perfect fit every time.
Outcome: With the new machine, Precision Seals Inc. reduced material waste by 40% and increased production speed by 50%. The improved accuracy and consistency led to higher customer satisfaction and a boost in repeat business.
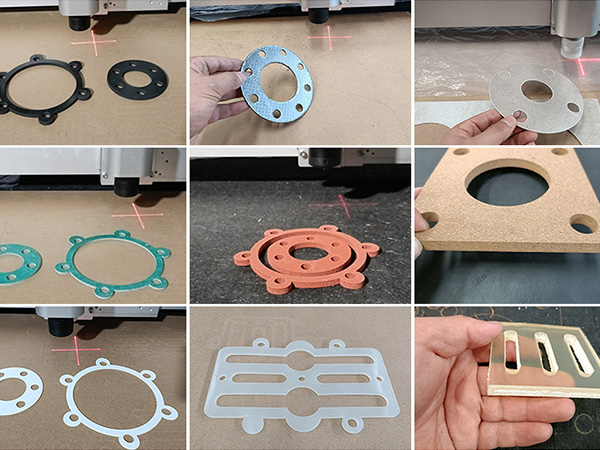
Custom Packaging Inserts at SecurePack Solutions
Industry: Packaging
Challenge: SecurePack Solutions needed to create custom foam inserts for their packaging, but their existing cutting processes were slow and imprecise. This resulted in high levels of waste and delayed production times.
Solution: We equipped them with a CNC foam cutting machine capable of cutting a variety of packaging materials, including foam and corrugated cardboard. The machine’s ability to make clean, precise cuts at high speeds was exactly what they needed.
Outcome: The machine helped SecurePack Solutions reduce material waste by 30% and cut production times in half. Their ability to quickly produce custom inserts not only improved packaging quality but also enhanced product protection during shipping.

Acoustic Panels at SoundWave Studios
Industry: Acoustic Solutions
Challenge: SoundWave Studios struggled to produce custom acoustic panels that met their client’s specific needs. Traditional cutting methods couldn’t handle the intricate designs or the variety of materials required.
Solution: We provided them with an oscillating knife-cutting machine that could effortlessly cut through polyester fiber, foam, and felt. This allowed them to create custom-shaped acoustic panels tailored to the unique acoustic needs of each room.
Outcome: The custom panels significantly improved sound quality in their studio spaces, leading to a 25% increase in client bookings. The ability to offer fully customized acoustic solutions also opened up new revenue streams for the studio.

Custom Footwear Production at Elite Footwear
Industry: Fashion (Footwear)
Challenge: Elite Footwear needed a more efficient way to produce custom leather shoes. Their old cutting methods were slow and often resulted in wasted material, which was costly and frustrating.
Solution: We introduced a CNC leather cutting machine that could handle leather and other synthetic materials with precision. The machine’s speed and accuracy allowed them to cut intricate patterns quickly, making it perfect for their custom designs.
Outcome: With the new machine, Elite Footwear reduced production time by 30% and decreased material waste by 20%. This efficiency boost allowed them to increase their production capacity and meet customer demand faster, leading to a 15% rise in sales.
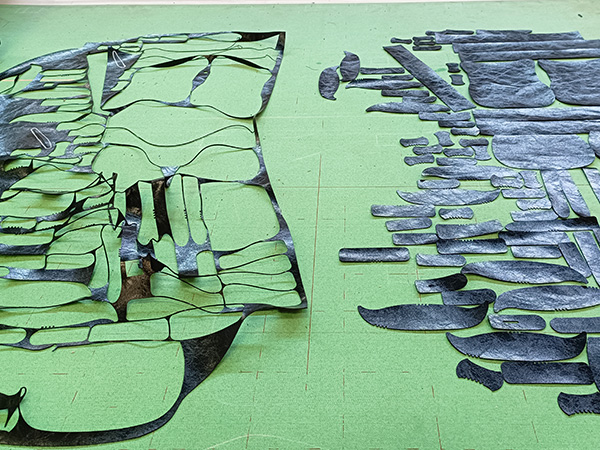
Soft Sofa Manufacturing at ComfortCouch Furnishings
Industry: Soft Furniture
Challenge: ComfortCouch Furnishings was facing difficulties in producing custom sofas. The variety of fabrics and the complexity of the designs required a cutting solution that was both flexible and precise. Their traditional cutting methods were too slow and inconsistent.
Solution: We provided them with a CNC fabric-cutting machine equipped with an oscillating knife. This machine could easily switch between different fabrics and handle complex patterns, making it ideal for their custom sofa production.
Outcome: The machine transformed its production process, reducing fabric waste by 25% and increasing production speed by 35%. ComfortCouch Furnishings could now fulfill custom orders more efficiently, leading to higher customer satisfaction and increased orders.

Conclusion
These case studies illustrate how AMOR CNC oscillating knife cutting machines are making a real difference across various industries. Whether it’s gaskets, packaging inserts, acoustic panels, footwear, or sofas, our machines help businesses overcome production challenges, reduce waste, and embrace smarter, more efficient manufacturing processes.