Alright, let’s get real—gasket production can be a bit tricky. Sure, gaskets are the unsung heroes in everything from engines to fridges, but making them? Not so simple. Luckily, CNC oscillating knife cutting machines have become the go-to solution for many manufacturers. But, how do you know which machine is the right fit for your gasket production? Well, that’s what we’re here to talk about. Grab a cup of coffee, and let’s go through the key features to look for when choosing the right CNC machine.
The Challenges of Gasket Production: It’s Not All Smooth Sailing
1. Machine Stability Woes
Ever had your machine shake, rattle, and roll while cutting through materials? Not ideal, right? Stability issues in older or poorly designed machines lead to inconsistent cuts. And when the cuts aren’t clean, you’re left with wasted materials or worse—gaskets that don’t fit right. That’s no good for anyone.
2. Cutting Complex Shapes: It’s Like Trying to Draw with Your Eyes Closed
When you need to cut complex shapes—like those custom gaskets that go into cars or specialized equipment—old-school machines just can’t keep up. They struggle with precision, making it hard to get the shapes exactly right. The result? Gaskets that don’t fit or need reworking. And let’s be honest, nobody has time for that.
3. Material Waste: More Waste, More Problems
Then there’s the waste. Old methods like die-cutting require molds, and you’re often stuck with unused material scraps. All that wasted material equals extra costs, and who needs that? It’s like buying a pizza and only eating half of it—what a waste!
4. Speed and Efficiency: Tick-Tock, Time’s Running Out
Speed is crucial in the manufacturing world. Tight deadlines are the norm, and slower machines only add pressure. If your machine can’t keep up, you’re going to fall behind on orders. And falling behind? Not an option when customers are waiting.
5. Inflexibility for Custom Orders: Stuck in the Past
These days, customers want custom orders in small batches, but traditional machines aren’t built for flexibility. They need molds, and molds take time and money. Trying to meet the demand for custom gasket shapes becomes a nightmare, not to mention expensive.

How CNC Oscillating Knife Cutting Machines Solve These Challenges
Now, let’s talk about how CNC oscillating knife cutting machines are a game-changer. These bad boys come with a ton of advantages that fix all those pesky problems you just read about.
1. Stability Like You’ve Never Seen
CNC oscillating knife machines are designed with stability in mind. They don’t shake or wobble around, no matter what material you throw at them. This means you get consistent, accurate cuts every single time. No more worrying about your gasket material shifting or ruining your cuts.
2. Cutting Complex Shapes: Easy Peasy
Got a tricky shape to cut? No problem. CNC machines are a dream when it comes to cutting custom gaskets. Whether it’s circles, zigzags, or something even more intricate, these machines handle it with ease. No need for molds, no mess. Just pure precision. You can even create those custom shapes for automotive or industrial use without breaking a sweat.
3. Bye-Bye, Material Waste
Thanks to intelligent nesting software, CNC machines make the most out of every material sheet. The software arranges the cuts so there’s barely any leftover material, helping you save money and cut down on waste. So, when you’re using your materials, you’re using them wisely.
4. Speed and Efficiency: Get Things Done Faster
CNC oscillating knife cutting machines don’t just cut accurately—they cut fast. Faster than traditional methods, meaning you can meet those tight deadlines and still deliver top-quality gaskets. No more delays or stress about falling behind. Time is money, and these machines help you save both.
5. Custom Orders? No Problem!
Need a custom gasket in a hurry? No need for molds or custom setups. CNC machines can handle small runs, quick adjustments, and last-minute orders with ease. Whether it’s a single custom piece or a batch of special orders, these machines are built for flexibility. Get it done quickly and efficiently—without the extra cost.
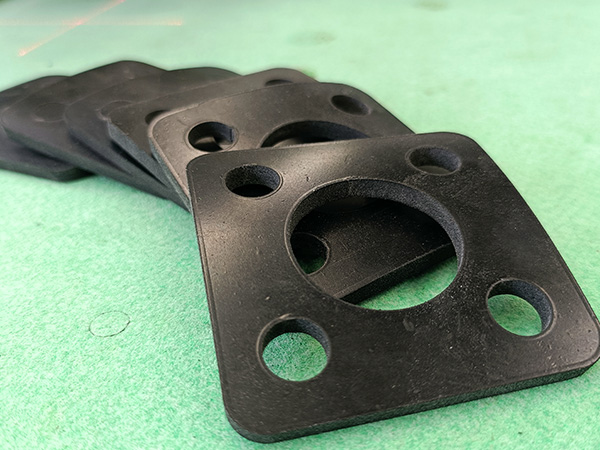
AMOR CNC Advantage: Why You Need the Best for Your Gasket Production
But hold up—let’s not forget: not all CNC machines are created equal. If you want the best results, you need to choose a high-quality machine. That’s where AMOR CNC comes in. Here’s why our machines are the real deal.
1. Sturdy Welded Bed for Stability
AMOR CNC machines come with a robust, welded bed that ensures the machine stays stable and balanced during operation. This means no shaky cuts, no issues with material shifting. You get top-notch precision every time.
2. High-Quality Electrical Components
When it comes to electrical components, we don’t cut corners. Our machines use Mitsubishi servo motors, Schneider Electric components, Omron limit switches, and Hiwin rails and racks. These high-end parts are what make our machines reliable and precise.
3. Scientific Mechanical Structure
AMOR CNC machines are engineered with a dual Mitsubishi servo motor-driven X-axis and precision bevel gear reducers. This combination ensures smooth and powerful operation, while also guaranteeing high-precision cuts. In other words, it’s strong, balanced, and accurate—just what you need.
4. Perfect Installation for Perfect Precision
We’ve perfected the installation process to make sure everything fits together just right. The X and Y-axis gears and racks have zero gaps, which means more accuracy and more consistent results. Every cut is as perfect as the last one.
5. Top-Notch Electrical Assembly
Our electrical assembly is top-tier. We use the same wire harness supplier as BYD Automotive, so you know the quality is unbeatable. Every wire is clearly labeled, and we even use barriers to prevent friction between them. It’s all about ensuring stability and long-lasting performance.
Real-World Success: How AMOR CNC Machines Changed the Game
Let’s wrap this up with a real-world success story. One of our clients in the sealing gasket industry had struggled with traditional machines that couldn’t keep up. They were facing issues with accuracy, wasted material, and slow production. After switching to an AMOR CNC oscillating knife cutting machine, everything changed. They cut faster, more accurately, and with less waste. The results? A huge boost in productivity, efficiency, and cost savings.
Conclusion: Ready to Upgrade Your Gasket Production?
There you have it! CNC oscillating knife cutting machines solve the toughest problems in gasket production—everything from machine stability to cutting complex shapes and reducing material waste. And with AMOR CNC machines, you get the best of the best: precision, reliability, and efficiency. So, if you’re looking to take your gasket production to the next level, it’s time to make the switch. Trust us, your future self will thank you.