Precision Cutting: The Key to Minimizing Material Waste
One of the primary benefits of CNC oscillating knife cutters is their ability to deliver precise cuts with minimal material waste. Traditional cutting methods, such as die-cutting or manual cutting, often lead to significant material loss due to inaccuracies and the need for wider cutting margins. In contrast, CNC oscillating knife cutters use advanced software to optimize the cutting path, ensuring that each gasket is cut with the utmost precision.
The oscillating knife tool moves rapidly back and forth, cutting through the material cleanly without dragging or distorting it. This precision not only reduces the amount of excess material that needs to be trimmed away but also allows manufacturers to nest multiple gasket designs closely together on a single sheet of material. This nesting capability maximizes material usage, resulting in less waste and more gaskets per sheet.
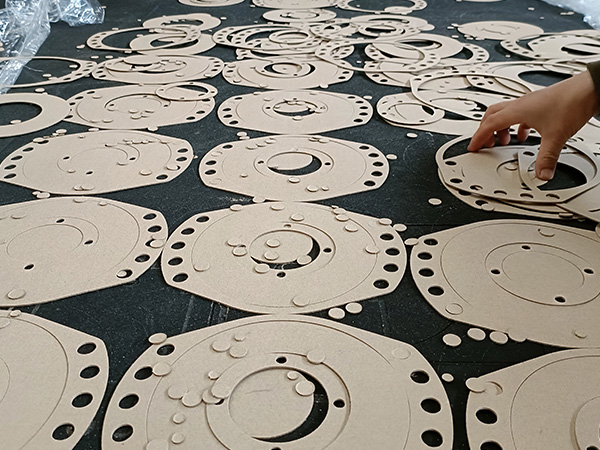
Versatility Across Different Materials
CNC oscillating knife cutting machines are designed to handle a wide range of materials, from soft rubber to high-density graphite reinforcement sheets. This versatility is crucial in gasket production, where different applications require different materials with varying thicknesses and properties. By using the appropriate cutting tool and machine settings, manufacturers can achieve clean, precise cuts across all types of gasket materials, further reducing waste that might occur with less adaptable cutting methods.
For instance, the 400W high-power electric oscillating tool is ideal for cutting dense, high-hardness materials like reinforced graphite, while the pneumatic oscillating tool is better suited for softer materials such as rubber or silicone. This ability to switch between tools and materials seamlessly enhances both the efficiency and quality of production.
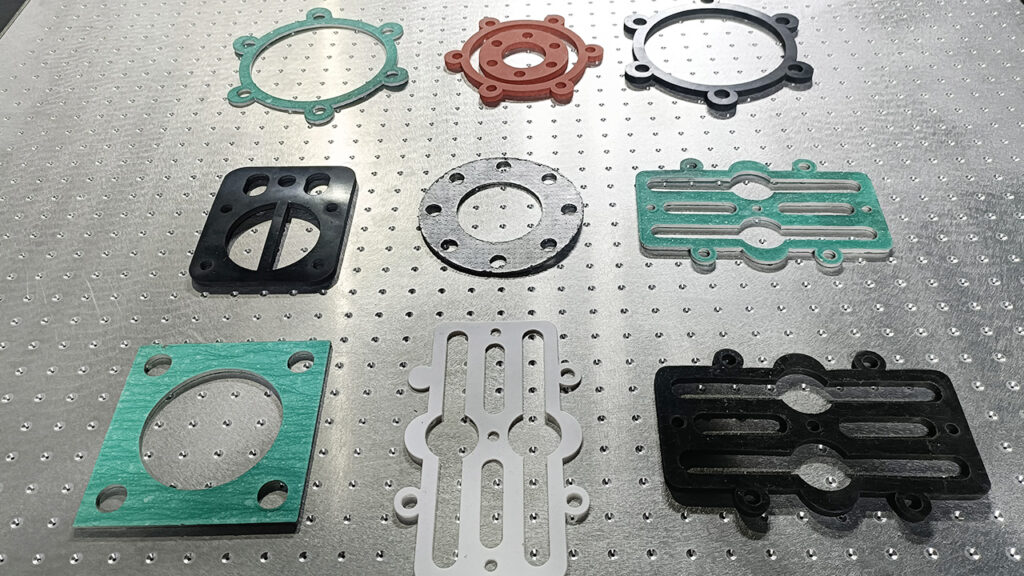
Streamlining the Production Process
Beyond waste reduction, CNC oscillating knife cutters significantly improve overall production efficiency. The automated nature of these machines allows for continuous operation with minimal manual intervention. Once a cutting job is set up and the material is loaded, the machine can run independently, cutting multiple gaskets with consistent accuracy and speed. This automation reduces the time required for manual adjustments, inspections, and rework, which are often necessary with traditional cutting methods.
Moreover, CNC oscillating knife cutters can handle complex gasket designs with intricate patterns and tight tolerances. The advanced software used in these machines can import digital designs directly, eliminating the need for physical templates or dies. This capability not only saves time but also ensures that design changes can be implemented quickly, without the delays associated with manufacturing new dies or reconfiguring manual cutting setups.
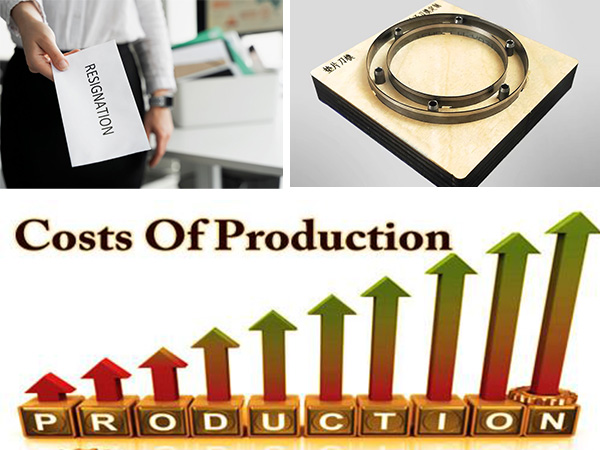
Reducing Rework and Rejects
In gasket manufacturing, rework and rejects are costly, both in terms of material waste and lost production time. CNC oscillating knife cutters drastically reduce the occurrence of these issues by ensuring that each cut is made with high precision and consistency. The likelihood of defects caused by inaccurate cutting is minimized, leading to fewer rejected pieces and less need for rework.
Additionally, the repeatability of CNC machines means that once a cutting job is perfected, it can be replicated exactly, no matter how many times it is run. This consistency is particularly valuable for large production runs, where even small deviations in cutting accuracy can lead to significant waste.
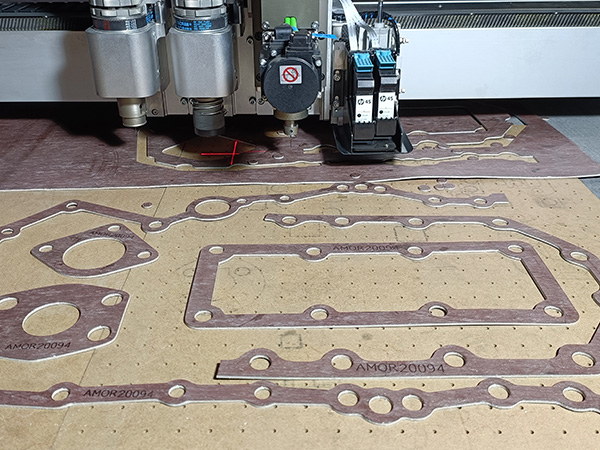
Conclusion: A Smart Investment for Gasket Manufacturers
Investing in CNC gasket-cutting machines is a smart move for gasket manufacturers looking to reduce waste and increase production efficiency. These machines offer unparalleled precision, versatility, and automation, all of which contribute to a more efficient and cost-effective production process. By minimizing material waste, reducing the need for rework, and streamlining operations, CNC oscillating knife cutters help manufacturers meet the demands of today’s market while maintaining high standards of quality and profitability.
For gasket manufacturers, the choice is clear: CNC oscillating knife cutting machines are not just a tool, but a strategic asset that drives efficiency and reduces costs across the production line.
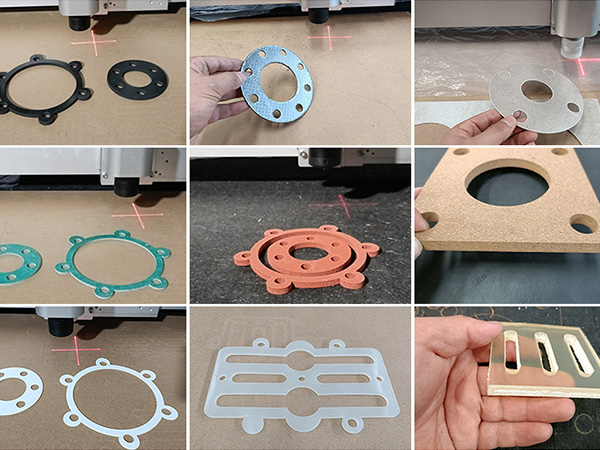