1. The Challenge: High Mix, Low Volume Production
Modern bag factories no longer make one style in bulk. They handle:
- Dozens of SKUs per season
- Frequent design updates
- Small orders for custom or limited-edition models
The problem: Traditional cutting methods like die-cutting can’t adapt fast enough. Each design change requires a new mold, which means added cost and longer lead times.
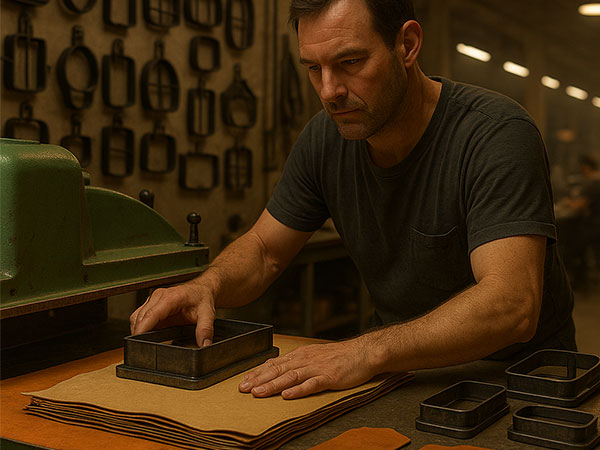
2. The Limitations of Traditional Leather Cutting
Let’s break it down:
Traditional Method | Pain Point |
---|---|
Steel die cutting | High tooling cost per design |
Manual hand cutting | Slow and inconsistent |
Design change | Time-consuming and inflexible |
Small batch production | Not cost-effective |
Bag brands need a solution that’s faster, smarter, and more adaptable.
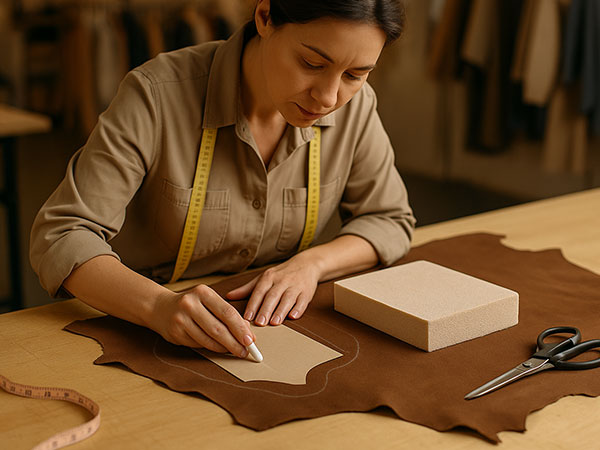
3. CNC Leather Cutting: On-Demand Flexibility
CNC leather cutters solve the above issues with digital precision.
No mold? No problem. Just load the new design file, and cutting begins instantly.
- Upload CAD patterns directly into the system
- Switch styles in seconds—no downtime
- Perfect for custom orders, prototype samples, and seasonal collections
✅ Result: Lower cost per design and faster turnaround.
4. Smart Nesting Maximizes Leather Usage
Natural leather is expensive—and never uniform. Irregular shapes, defects, and natural grain lines make it hard to cut efficiently by hand.
With CNC cutting:
- Vision systems scan each hide in detail
- Nesting software arranges pieces to avoid flaws and use every usable inch
- Patterns are placed based on real-time data, not guesswork
✅ Result: Less leather waste, lower material cost, and higher profit margin.

5. Rapid Response to Design Trends
New trend this month? Limited drop next week?
With CNC leather cutters, you don’t need to wait for new molds. The machine:
- Instantly loads new patterns
- Starts cutting immediately
- Supports daily or weekly model changes
✅ Result: You stay ahead of fashion cycles and customer demand—without delay.
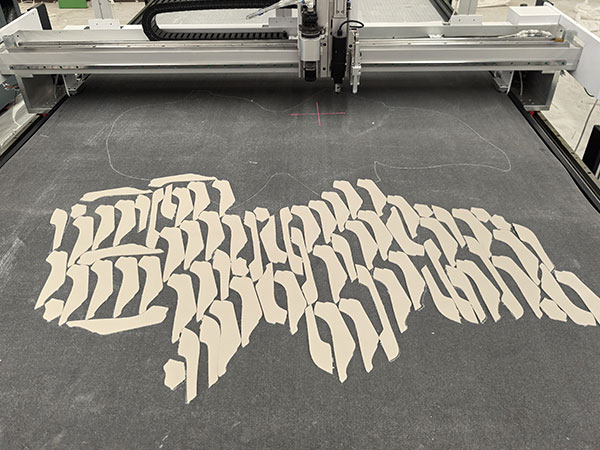
6. Ideal for Small-Batch and Custom Orders
More brands now offer:
- Made-to-order bags
- Monogrammed designs
- Limited-edition collections
Traditional cutting is too slow and costly for such production.
CNC machines make it simple:
- Cut as few as one piece—no extra setup
- Handle different sizes, shapes, and styles in one batch
✅ Result: Full flexibility, no waste, and zero tooling investment.
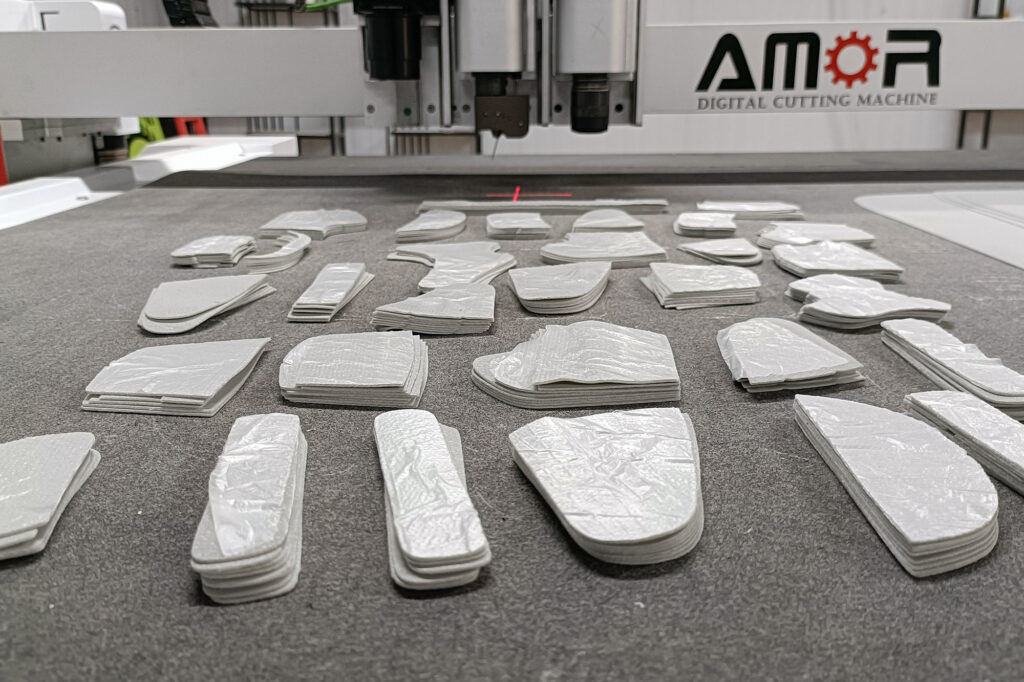
Conclusion: Smarter Bag Manufacturing Starts Here
CNC leather cutting machines empower bag manufacturers to meet modern demands: speed, flexibility, and customization. From precise cutting to real-time nesting, they streamline production while reducing costs and waste.
Key Benefit | Impact |
---|---|
No mold required | Instant design switching |
Smart nesting | Max leather use, minimal waste |
On-demand cutting | Fast delivery for small orders |
High precision tools | Consistent quality every time |
Digital control | Easy integration with design software |
Final Thoughts
For bag manufacturers looking to upgrade, CNC leather cutting machines are no longer optional—they’re essential. Whether you’re producing luxury handbags, custom backpacks, or seasonal purses, these machines help you move faster, cut smarter, and serve customers better.
Let AMOR CNC help you build a flexible, future-ready production line—designed for modern leather goods.