Client Story: An Indian Customer’s Experience with AMOR CNC
AMOR CNC, a leading manufacturer of CNC oscillating knife cutting machines, recently helped an Indian customer enhance their production capabilities by providing a state-of-the-art solution for cutting high-density insulating paperboard. The customer, a key player in the electrical insulation industry, sought a machine that could deliver precision, efficiency, and cleanliness in cutting 1-3mm thick insulating hard paperboard.

Selecting the Right Tool: The 400W Oscillating Knife Cutter
After thorough consultations and evaluations, the customer selected AMOR CNC’s 400W oscillating knife-cutting machine. This powerful tool was chosen for its ability to cut through high-density insulating paperboard with ease and precision. The key features that influenced this decision included:
Precision Cutting: The 400W oscillating knife cutter delivers highly accurate cuts, essential for maintaining the insulating properties of the hard paperboard.
Smooth Cut Edges: The machine ensures smooth, clean cut edges without fraying or tearing, preserving the material’s integrity and functionality.
Dust-Free Operation: Unlike traditional cutting methods, the oscillating knife cutter operates without generating dust, creating a cleaner and safer working environment.
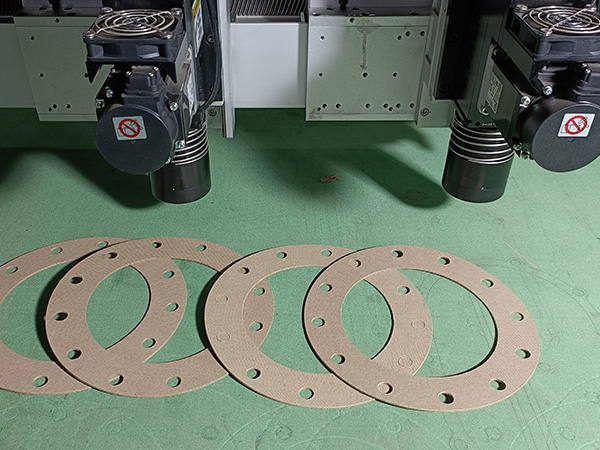
Enhancing Efficiency with Dual 400W Oscillating Tool Heads
To further optimize their production process, the customer adopted a dual-head configuration, featuring two independent 400W oscillating tools. This setup allowed for simultaneous operation of both cutting heads, significantly boosting productivity. The advantages of this configuration included:
Increased Efficiency: With two cutting heads working simultaneously, the customer could double their output, reducing production times and increasing overall efficiency.
Flexibility and Customization: The dual-head setup provided the flexibility to cut same shapes and sizes concurrently, catering to various design requirements without frequent tool changes.
Cost Savings: The enhanced efficiency and reduced production times led to considerable cost savings, making the investment in AMOR CNC’s technology highly cost-effective.
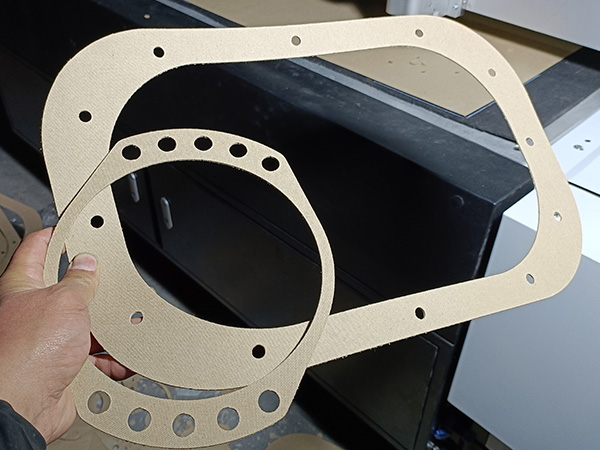
Comparing Oscillating Knife Cutting to Other Methods
- Manual Cutting: Utility Knives and Scissors: Manual methods are labor-intensive, less precise, and unsuitable for high-volume production. They also risk uneven cuts and material damage.
- Mechanical Cutting: Guillotine and Rotary Cutters: While they offer straight cuts, these methods lack the flexibility to handle complex shapes and often require manual adjustments, slowing down the process.
- Laser Cutting: CO2 Laser Cutters: Laser cutting provides precision but can generate heat, risking burning or discoloration of the paperboard edges. Additionally, it may produce fumes and require ventilation systems.
- Die Cutting: Flatbed and Rotary Die Cutting: Effective for high-volume, repetitive shapes, but the initial cost for dies can be high, and the process lacks flexibility for custom or small-batch orders.
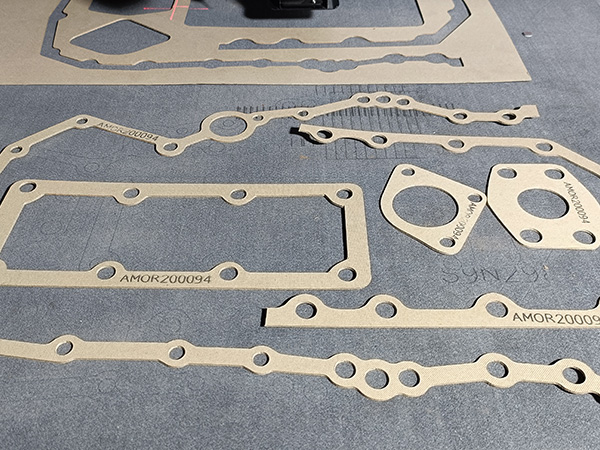
Advantages of Oscillating Knife Cutting:
High Precision: Provides clean, accurate cuts for complex and intricate designs.
No Heat Generation: Avoids the risk of burning or discoloration, preserving material quality.
Dust-Free Operation: Maintains a clean workspace, enhancing safety and reducing cleanup time.
Flexibility: Easily programmable for various shapes and sizes without the need for new dies or significant adjustments.
Cost-Effective: Reduces material waste and eliminates the need for expensive dies, making it ideal for both small and large production runs.
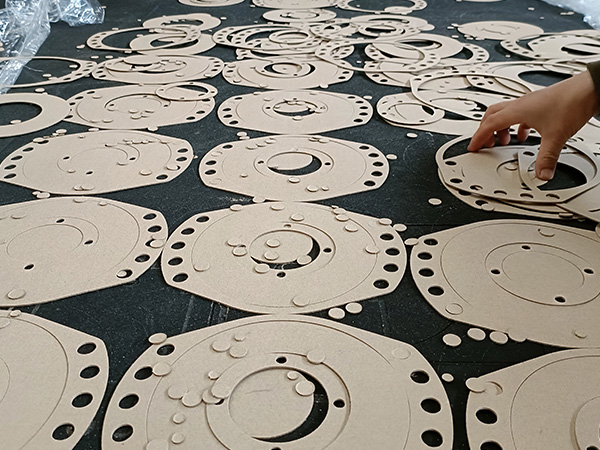
Conclusion: A Satisfied Customer
The Indian customer was highly satisfied with their investment in AMOR CNC’s 400W oscillating knife cutting machine. The machine’s ability to deliver precise, smooth, and dust-free cuts of 1-3mm high-density insulating hard paperboard met and exceeded their expectations. The dual-head configuration proved to be a game-changer, significantly enhancing their production capabilities and efficiency.
This success story underscores AMOR CNC’s commitment to providing advanced, customizable, and high-quality cutting solutions that meet the specific needs of its clients across various industries. As a result, AMOR CNC continues to be a trusted partner for businesses seeking to improve their manufacturing processes and product quality.