10 Advantages of Using a CNC Genuine Leather Cutting Machine Over Traditional Cutting Methods

Hello, I’m an AMOR CNC technical engineer, and I’ve seen firsthand how CNC leather cutting machines can transform a leather workshop. If you’re still using traditional cutting methods, it’s time to consider the upgrade. Let me walk you through why CNC cutting machines are a game-changer and how they stack up against the old-school ways.
How Do Automatic Fabric Cutting Machines Improve Efficiency and Reduce Waste for Upholstered Sofas

Ever watched piles of fabric scraps grow higher and higher on your workshop floor? Frustrating, isn’t it? As an engineer at AMOR CNC, I’ve seen firsthand how inefficient cutting processes can eat into profits and test your patience.
But here’s the silver lining: Automatic Fabric Cutting Machines are transforming the game. These technological marvels speed up production and slash waste, making your upholstered sofa manufacturing process smoother than ever.
Curious how this all works? Let’s dive in and explore.
The Benefits of Using a CNC Fabric Cutting Machine in Upholstered Furniture Manufacturing

In the competitive world of upholstered furniture manufacturing, efficiency and precision are paramount. As consumer demand for high-quality, stylish furniture grows, manufacturers are turning to advanced technologies to stay ahead. One such innovation making a significant impact is the CNC fabric cutting machine. This technology revolutionizes the way fabric is cut and processed, offering numerous benefits that enhance production and product quality.
Transforming Efficiency: Unleashing the Power of AMOR CNC Gasket Cutting Machines for Enhanced Productivity

In the competitive landscape of modern industry, efficiency and precision are paramount. Gaskets, though often overlooked, play a critical role in the functionality and safety of countless machines and devices. Enter AMOR CNC, a leader in innovative cutting solutions, whose oscillating knife gasket cutting machines are revolutionizing the gasket manufacturing industry.
How To Custom Cut EPE Foam with a CNC Oscillating Knife Cutting Machine in 5 Simple Steps

To begin, you’ll need:
EPE Foam (also known as Expanded Polyethylene Foam)
CNC Oscillating Knife Cutting Machine
Your digital design file
Measuring tape or calipers
The equipment you want to fit.
For this demonstration, we’ll guide you through customizing EPE foam inserts using a CNC machine to achieve a perfect fit for your products.
Step-by-Step Guide: How to Using an Automatic Fabric Cutting Machine for Upholstery Sofa

If you’ve ever been part of the upholstery business, you know that manual fabric cutting is time-consuming and, let’s be honest, sometimes downright frustrating. Precision is key, but human errors can slip in, and the material wastage can add up. This is where an automatic fabric cutting machine for sofas steps in and saves the day. It takes your sofa production to the next level.
At AMOR CNC, we’ve developed a complete solution for automating fabric cutting that’s easy to use and saves time and fabric. This guide will take you through the process, step-by-step, so you can see exactly how to implement this technology into your sofa production line.
In this post, I’ll share my expertise as an engineer, so you get the real inside scoop on making your fabric cutting process fast, smart, and worry-free!
PTFE Gasket Cutting Machine: Why Is Precision So Important?
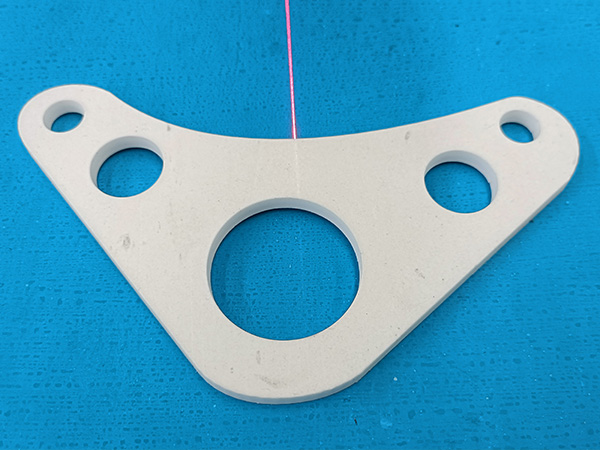
If you’re involved in manufacturing, especially in the production of gaskets, you probably know just how critical PTFE gaskets are. Whether it’s for their excellent chemical resistance, high-temperature stability, or low friction, PTFE (Polytetrafluoroethylene) gaskets offer everything industries like chemical processing and automotive need. But how do you ensure precision when cutting these gaskets? That’s where a PTFE gasket cutting machine comes in.
A PTFE gasket cutting machine takes all the guesswork out of gasket production, allowing you to cut with speed, accuracy, and efficiency. It’s a must-have for businesses that want to maintain high standards in manufacturing.
Keep reading, and I’ll show you how investing in the right cutting machine will not only save you time but also reduce waste and improve overall efficiency.
The Ultimate Guide to AMOR CNC Rubber Gasket Cutting Machines: Precision, Efficiency, and Customization
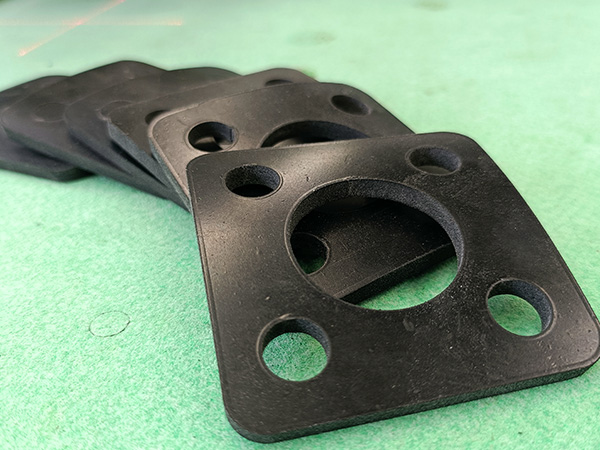
Rubber gaskets are essential components in a wide range of industries, from automotive and aerospace to plumbing and industrial manufacturing. These gaskets create airtight seals between two surfaces, preventing leaks and ensuring long-lasting performance.
As the demand for custom gasket shapes and sizes increases, traditional cutting methods often fall short. This is where AMOR CNC Rubber Gasket Cutting Machines come into play, offering precision, efficiency, and the flexibility to cut complex designs without the need for molds.
In this guide, we’ll explore how AMOR CNC machines are revolutionizing rubber gasket production, making it easier for manufacturers to meet modern requirements with superior quality and speed.
Why is a CNC Foam Cutting Machine Essential for Custom Foam Packaging Inserts?

Ever wonder why the packaging industry keeps talking about custom foam inserts? It’s not just because it sounds fancy. The real reason is that foam inserts can make or break your product’s journey from point A to point B. Think about the last time you received a fragile item. Did it arrive in one piece? If so, you probably have foam packaging to thank for that.
In industries like electronics, medical devices, and automotive, custom foam inserts are the unsung heroes of product protection. They’re tailored to your product’s exact shape, ensuring everything stays snug and secure. You don’t want your delicate electronics bouncing around in transit, right?
And that’s where my trusty CNC oscillating knife machines come into play. They’re designed to create these foam inserts quickly, accurately, and without any hassle.
What is the difference Between Pneumatic and Electric Oscillating Tools When Cutting Polyester Fiber Acoustic Panels?

Choosing the right tool for cutting thick polyester fiber panels can feel like trying to decide between a heavy-duty truck and a sports car. Both get the job done, but in very different ways. When it comes to selecting between pneumatic and electric oscillating tools, understanding their strengths and limitations will help you make the right decision for your project.
In short, pneumatic oscillating tools are ideal for cutting thicker, denser panels (24-50mm), thanks to their greater power. On the other hand, electric oscillating tools excel in speed and precision, especially when working with thinner panels (9-12mm). Each tool has its specific application, but they can also be used together to cover a range of material thicknesses.
Now, let’s dive deeper into how these two types of tools perform when cutting polyester fiber sound-absorbing panels and why you might choose one over the other.