Incorrect Tool Selection
Choosing the wrong tool for the material you’re working with is a mistake I see often. Every material has its quirks—whether it’s rubber, foam, or corrugated cardboard—and using the wrong tool can lead to poor results or even damage your machine.
How to Avoid It:
Match the tool to the material. For example, if you’re cutting large sheets of corrugated cardboard, go with the high-frequency electric oscillating tool. For honeycomb cardboard, the pneumatic oscillating tool is your best bet.
When in doubt, check the machine’s manual or reach out to us for guidance. We’re here to help!


Inadequate Maintenance
Machines are like cars—they need regular upkeep to run smoothly. Skipping maintenance can lead to all sorts of problems, from dull blades to complete machine breakdowns.
How to Avoid It:
Set up a regular maintenance schedule. This should include cleaning the machine, checking the blades for wear, and replacing any worn parts.
After each use, take a moment to clean the cutting tool with an air gun. It only takes a minute and can make a big difference in performance.
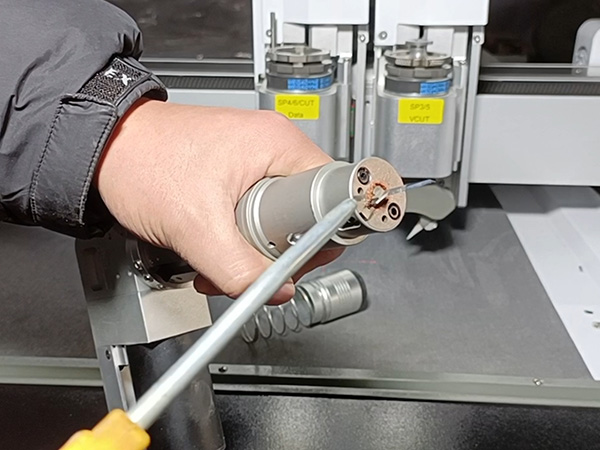
Improper Material Support
I can’t tell you how many times I’ve seen cuts go wrong because the material wasn’t properly supported. If your material shifts or isn’t firmly in place, you’re in for a rough cut.
How to Avoid It:
Always activate the vacuum adsorption and zoned adsorption systems on your cutting table. These features are designed to keep your material locked down tight during the cutting process.
For extra security, especially with large or oddly shaped materials, use clamps or other supports.

Incorrect Cutting Speed
Running the machine at the wrong speed can cause all sorts of issues, from jagged edges to incomplete cuts. Different materials require different cutting speeds, so it’s crucial to get this right.
How to Avoid It:
Adjust the cutting speed based on the material and the tool you’re using. For example, when cutting thin rubber sheets with the high-frequency electric oscillating tool, you can crank up the speed to around 1200mm/s.
Start with a moderate speed and tweak it based on how the material responds.

Overlooking Safety Precautions
It’s easy to get comfortable and start skipping safety steps, but this is a big no-no. Not only does it put you at risk, but it can also damage your machine.
How to Avoid It:
Always follow the safety guidelines: wear your protective gear, make sure the machine is grounded, and never bypass safety interlocks.
Keep your work area tidy and free from hazards that could cause accidents.

Ignoring Blade Sharpness
A dull blade is a recipe for disaster. It can cause your cuts to be rough and uneven, and it puts unnecessary strain on your machine. Worse yet, if the blade isn’t installed correctly—with the sharp side oriented the right way—you’ll end up wasting a lot of material.
How to Avoid It:
Regularly check your blades for sharpness. If they’re looking dull, it’s time to swap them out.
When installing a new blade, double-check that it’s positioned correctly, with the sharp edge ready to do its job. This simple step can save you a lot of headaches—and material!

Inadequate Training
Even the best machine can’t make up for a lack of know-how. If your operators aren’t properly trained, you’re going to run into problems.
How to Avoid It:
Make sure everyone who uses the machine has been thoroughly trained. This includes knowing how to select the right tool, adjust the speed, and perform routine maintenance.
Offer refresher courses or updates whenever new tools or techniques are introduced. Staying sharp on your skills is just as important as keeping your blades sharp!
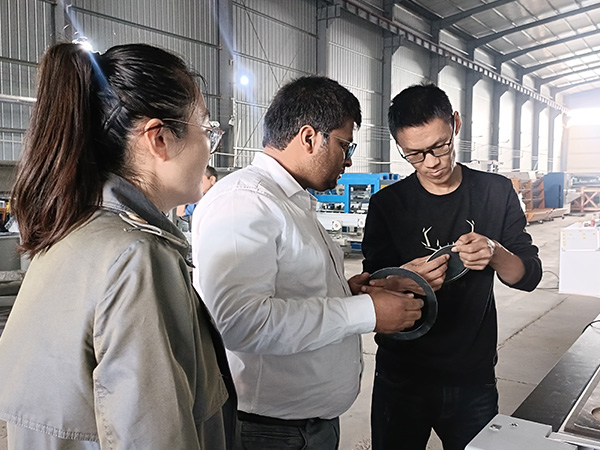
Neglecting Software Updates
Your machine’s software controls a lot of its functions, and skipping updates can lead to performance issues or compatibility problems with new tools.
How to Avoid It:
Regularly check for and install software updates from the manufacturer. These updates often include important fixes and new features that can improve your machine’s performance.
Keep the software and firmware up to date to make sure everything runs smoothly and efficiently.

Conclusion
By avoiding these common mistakes, you’ll get the most out of your oscillating knife cutting machine. Remember, it’s all about the right tools, proper maintenance, and staying sharp—literally and figuratively! At AMOR CNC, we’re here to support you every step of the way. Whether you need advice on tool selection, help with maintenance, or training for your team, we’ve got you covered.
If you ever have any questions or run into issues, don’t hesitate to reach out. We’re here to help you cut through the challenges and keep your production line running like a well-oiled machine. Happy cutting!