Problem 1: Uneven or Ragged Edges
This is the most frequent complaint. The edge looks wavy, torn, or just plain messy.
Causes include:
- Wrong blade angle or poor installation—especially by new operators. If the blade edge doesn’t face the cutting direction, expect trouble.
- Cutting too fast relative to oscillation frequency. For example, a 400W tool runs at 4000 strokes/min. That’s powerful, but if you cut hard materials like non-asbestos at 150mm/s, the tool can’t keep up—resulting in ripple-like edges. We recommend 50–70mm/s for optimal results.
- Worn internal tool components (e.g., transmission shaft or blade clamp) causing vibration and irregular motion.
- Clean lines on straight cuts but messy bolt holes? That’s likely due to slow cutting speed in circular paths combined with a blade that’s too wide.
AMOR’s Fix:
- Blade installation guides with diagrams to prevent direction errors.
- Pre-configured speed-frequency settings tailored to each tool.
- High-rigidity tool holders with tight tolerances.
- A wide selection of blade angles (16°, 30°, straight-edge) for different shapes and materials.
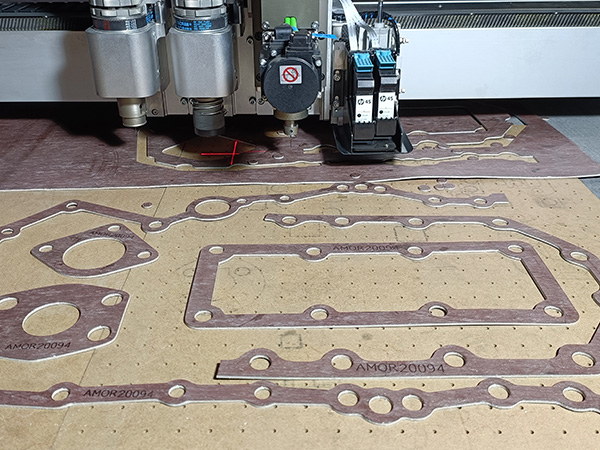
Problem 2: Inconsistent Cutting Depth
Sometimes the blade cuts too deep, sometimes not deep enough—even within the same piece.
Likely causes:
- Unstable air pressure (below 0.6 MPa) for pneumatic tools. Pressure fluctuation = depth fluctuation.
- Platform flatness deviation. A poorly machined cutting table can introduce height differences across the sheet, affecting depth. For example, a 1600×2500mm platform must have a ≤0.5mm height tolerance from edge to edge.
AMOR’s Fix:
- Pressure regulation systems and training on pneumatic tool use.
- Every machine platform is tested for flatness before shipment—no surprises on arrival.

Problem 3: Material Shifting or Stretching During Cutting
This usually shows up as offset cuts or distorted gasket shapes.
Common causes:
- Inadequate vacuum hold-down or failure to enable zoned adsorption. Small materials placed on a large table won’t stay put without it.
- Blade orientation mistakes or use of low-amplitude tools on elastic materials like rubber can lead to stretching during cutting.
AMOR’s Fix:
- Zoned vacuum table with strong suction across all regions.
- Setup guidance for blade direction and tool amplitude matching based on material elasticity.
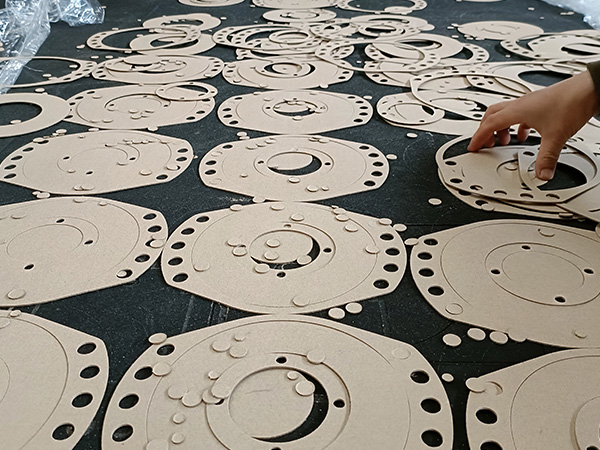
Problem 4: Blade Wear or Breakage
Blade breaks mid-job? Wears out too fast? That’s not normal.
Why this happens:
- Speed too high when piercing material, or too fast during complex cuts.
- Wrong tool selected—400W or pneumatic tools are a must for hard gaskets.
- Blade breaks near edges? Likely poor suction causing material movement.
- Using the wrong blade length or omitting a blade cap, which provides pressing support during cuts.
AMOR’s Fix:
- Material-specific blade/tool recommendations.
- Optional blade caps for added cut stability.
- Stronger vacuum + right blade length = fewer broken tips.

Problem 5: Small Holes or Circles Not Fully Closed
Bolt holes are the perfect shape… except they don’t close.
Causes include:
- X/Y/Z axis backlash—if there’s mechanical play, your start and endpoint won’t align.
- Loose sliders on guide rails or lightweight blade holders not suited for high-vibration materials like non-asbestos.
- W-axis belt damage—worn teeth or stretching will throw off the rotation angle.
AMOR’s Fix:
- Heavy-duty reinforced blade holders for hard material applications.
- Precision-milled racks and gears with minimal backlash.
- Narrow, high-precision blades (e.g., 16° tip) recommended for hole cutting.
- Reliable W-axis components with durable, reinforced belts.

Problem 6: Dimensional Inaccuracy or Inconsistency
You cut ten of the same gasket… and they all have slightly different dimensions.
Why this happens:
- Blade is off-center in the tool, so all cuts are misaligned.
- Structural machining error in the machine bed or loose gear engagement.
- Belt drive issues—if the drive belt stretches or slips, it throws off step accuracy. This is why belt-only systems are risky for cutting high-resistance materials.
AMOR’s Fix:
- Centralized blade alignment protocols.
- Precision-machined frame and gear systems, not mass-produced shortcuts.
- Gear reducer transmission systems preferred over belt drives for dimensional stability.

Conclusion
Using a CNC oscillating knife cutting machine for gasket production can unlock powerful productivity and accuracy—but only if the machine is engineered right and operated correctly.
Many problems arise from inexperienced use, but a surprising number stem from poor machine structure, component quality, or improper configuration. That’s why it’s so important to evaluate not just the price—but the machine design, control system, and vacuum platform.
✅ Our advice:
- Choose a machine with a solid structural design and proven mechanical engineering.
- Request professional training during setup.
- Communicate regularly with your machine supplier when problems arise—don’t try to troubleshoot everything alone.
- And most importantly, gain experience over time to truly unlock the value of CNC cutting technology.